Hardware Model:
The manipulation system consists of a a gripper model attached to the bottom of the drone. It was designed using solidworks. The image below shows the picture of the design.
The design was specifically done in order to tackle the different types of stress and strain issues that will occur because of 3D printing.
Below is the physically manufactured part printed with Black Nylon material.
Working:
- In order to conserve battery, Electro Permanent magnets were used instead of electro magnets as the gripper mechanism.
- The gripper mechanism is triggered using PWM signals which can be produced using a micro-controller.
- Arduino is beFINAL MANIPULATOR DESIGN :ing used for the initial tests and it will be replaced by Teensy in the future to facilitate the reduction in size and weight.
Gripper in simulation:
Considering the fact that we had to move to simulation because of the unfortunate COVID-19 outbreak, the following is the progress made with respect to manipulation as a part of the simulation subsystem.
- The magnetic gripper is based on a plugin that uses the magnetic dipole-dipole model to compute the force and torque between multiple magnets.
- The plugin is enabled per model and looks for other models in the gazebo world that have the same plugin.
- It only simulates magnetic interactions between magnets.
FINAL PACKAGE DESIGN :
FINAL MANIPULATOR DESIGN :
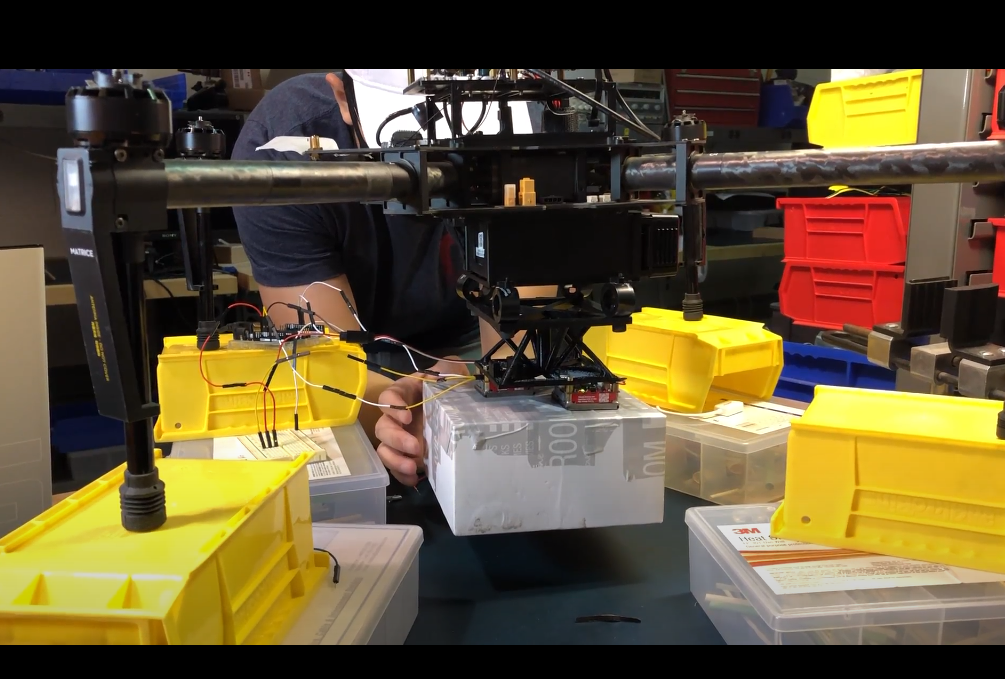