Fall Performance Evaluation:
Our objective for our Fall Validation Demonstration is to combine all subsystems into an autonomous aerial delivery system. These subsystems being the software subsystem, manipulation subsystem, sensing subsystem, navigation subsystem and planning subsystem. The demonstration was performed at the grass field on the Cut at Carnegie Mellon University. A video of a full run of the system is shown in the Final Video.
Procedure:
- An operator places a single box with an AprilTag on top at a predefined location.
- The operator places the drone at a predefined location.
- The ground station sends a pickup request to the drone.
- The drone takes off and flies to the package location.
- The drone detects and localizes the package.
- The drone picks up the package and flies to the platform.
- The drone detects and localizes the platform.
- The drone drops off the package on the platform.
As shown below, we have met almost all of our fall validation demonstration requirements, with an asterisk on the drop-off success rate. The Fall Validation Demonstration video is linked in the reference.
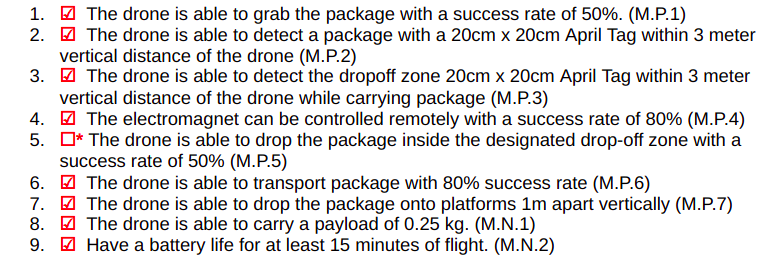
We were able to grasp the package with a 100% success rate during our FVD encore. One of the attempts was halted due to the magnets not being turned on prior to the takeoff, yet that is more of human negligence rather than a system issue. If we take that mistake into account, we still make our validation goal of the gripping success rate of 50% with at 80%, and the electromagnet controls success rate also at 80%. For the drop-off, our drone arrived at the platform two times in total. Once the package missed the platform completely, and the other time the package dropped into the platform but it bounced off on to the ground. Thus, although we were able to demonstrate the capability of our system’s platform tracking ability, we did not count the bounce-off as a successful attempt. As for the transporting requirements, the 0.25 kg package did not drop during all the attempts where the package was successfully gripped, so (M.P.6) and (M.N.1) are fulfilled.
Spring Performance Evaluation:
In the Spring semester, we first implemented our system in simulation and evaluated the requirements based on our simulated system. As shown below, we have met all of our Spring validation demonstration requirements, with one caveat being the localization positional precision. The Spring Validation Demonstration video can also be found in the Media Tab.
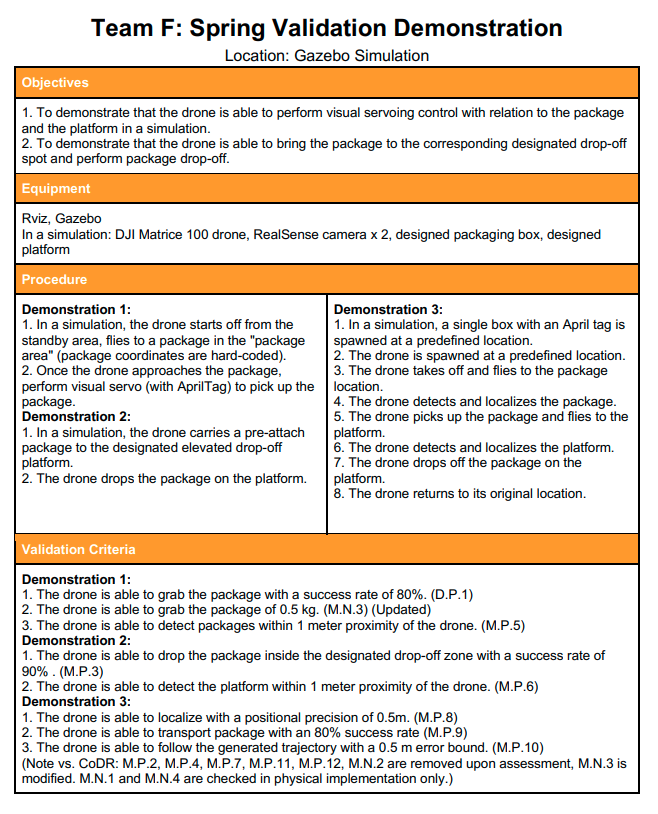
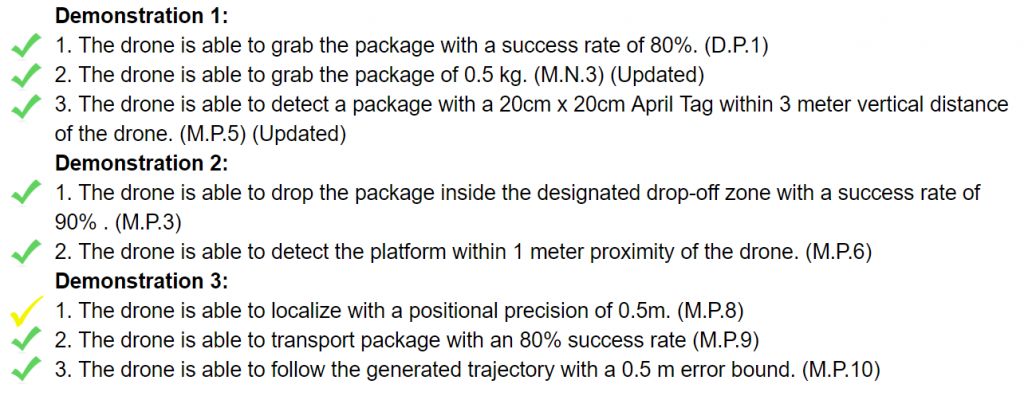
We are able to move to the pickup location, visual servo on to the package and grab it with 100% success rate after 20 tries. We are also able to drop the package onto the platform with 95% success rate.
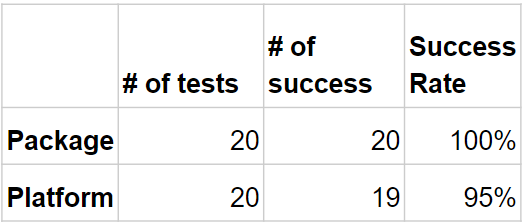
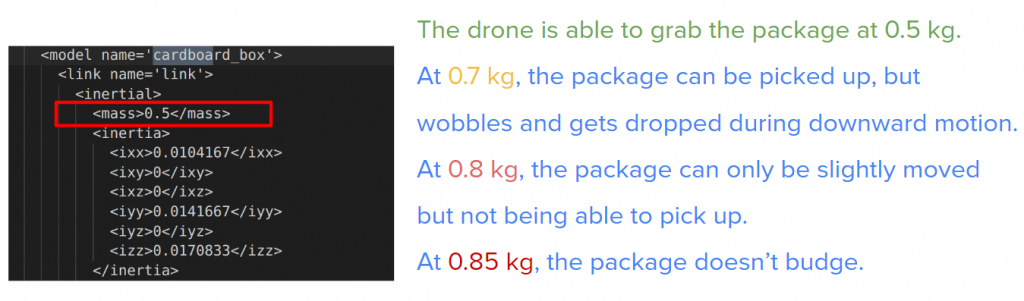
Navigation subsystem:
To satisfied M.P.10, the drone is able to follow the generated trajectory with a 0.5 m error bound, we tuned the PID parameters. The trajectory tracking results are shown in figure below. The Y axes of the plots are tracking error, which is the difference between tracking point and robot odometry. As we can see, all of them are under 0.5 meter.