Cyberphysical Architecture
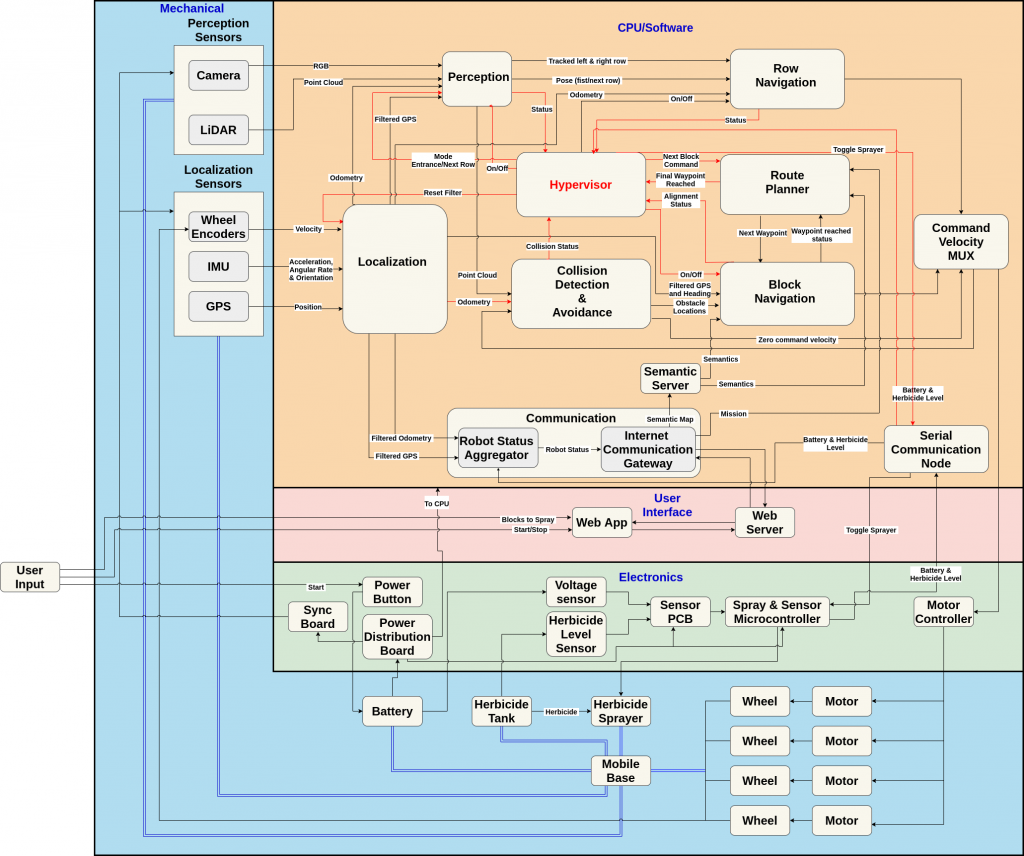
Mechanical
The mechanical subsystem comprises the chassis, spraying mechanism, and mounts for all the sensors and computing unit. The mobile base chosen according to the trade study is a Husky from ClearPath robotics, so no work needs to be done from a mechanical standpoint to get the platform running. Similarly, the development work for the sprayer and its mounting mechanism has been alleviated since our end-user is developing it.
Electronics
The electronics subsystems consist of the following components:
- Power distribution board to deliver power to all the sensors, computing unit, and spraying mechanism. The Husky comes preconfigured with this and provides outputs of 5V, 12V, 24V fused at 5A each, which would be sufficient for our requirements.
- Voltage and herbicide level detection sensors feed into a microcontroller to relay the status to the compute unit. The microcontroller will also be used as a relay by the computing unit to toggle the sprayer when needed. The voltage sensor already comes integrated with the Husky, so we will be using that instead of developing our solution.
- Synchronization board to trigger and synchronize the data coming from all the sensors. This is optional and will only be pursued if the need arises and time permits.
User Interface
- The web UI will allow the user to monitor the current status of the robot, including the current location, battery and herbicide level, and a report of the blocks it has already sprayed. The user would also be able to send commands to the robot using the same UI regarding which blocks to spray or stop the robot if something goes wrong.
- The web server acts like a relay between the UI and the robot, allowing for asynchronous communication, enabling the robot to send its status periodically. This status information is then cached on the server and delivered to the user when requested. This allows for a more robust communication mechanism since there may be periods of internet disruptions in which the robot will not be able to connect to the internet. During these periods, the user will still be able to see the robot’s last status, removing the need for the UI to be constantly connected to the robot.
Software
The software subsystem has eight major components:
Perception, Localization, Row Navigation, Block Navigation, Communication, Route Planner, Hypervisor, Collision Detection
The last three are of low priority and can be dropped in case of time constraints. We will also be outsourcing the communication subsystem to focus more on autonomy and delivering complete functionality. These computations are being done on a mini PC powered by a Ryzen 4800U with 16GB of RAM.
We purposefully made a very detailed cyberphysical architecture to identify the complexity of each component and potential issues we might encounter which would affect our schedule. Secondly, it allowed us to make the architecture modular so that low-priority components can be dropped or outsourced if we are constrained by time.
- to the compute unit. The microcontroller will also be used as a relay by the computing unit
- to toggle the sprayer when needed. The voltage sensor already comes integrated with the
- Husky, so we will be using that instead of developing our solution.
- 3. Synchronization board to trigger and synchronize the data coming from all the sensors. This
- is optional and will only be pursued if the need arises and time permits.
- 6.3 User Interface
- The user interface subsystem can be broken down into two components:
- 1. The web UI will allow the user to monitor the current status of the robot, including the current
- location, battery and herbicide level, and a report of the blocks it has already sprayed. The
- user would also be able to send commands to the robot using the same UI regarding which
- blocks to spray or stop the robot if something goes wrong.
- 2. The web server acts like a relay between the UI and the robot, allowing for asynchronous
- communication, enabling the robot to send its status periodically. This status information
- is then cached on the server and delivered to the user when requested. This allows for a
- more robust communication mechanism since there may be periods of internet disruptions
- in which the robot will not be able to connect to the internet. During these periods, the user
- will still be able to see the robot’s last status, removing the need for the UI to be constantly
- connected to the robot.
- 6.4 Software
- The software subsystem has eight major components: Perception, Localization, Row Naviga-
- tion, Block Navigation, Communication, Route Planner, Hypervisor, Collision Detection
- The last three are of low priority and can be dropped in case of time constraints. We will also
- be outsourcing the communication subsystem to focus more on autonomy and delivering complete
- functionality. These computations are being done on a mini PC powered by a Ryzen 4800U with
- 16GB of RAM.
- We purposefully made a very detailed cyberphysical architecture to identify the complexity
- of each component and potential issues we might encounter which would affect our schedule.
- Secondly, it allowed us to make the architecture modular so that low-priority components can be
- dropped or outsourced if we are constrained by time