Latest System Status
——————— Sept 2022 ———————
https://www.youtube.com/watch?v=cohBpv56dSo
——————— Feb 2022 ———————
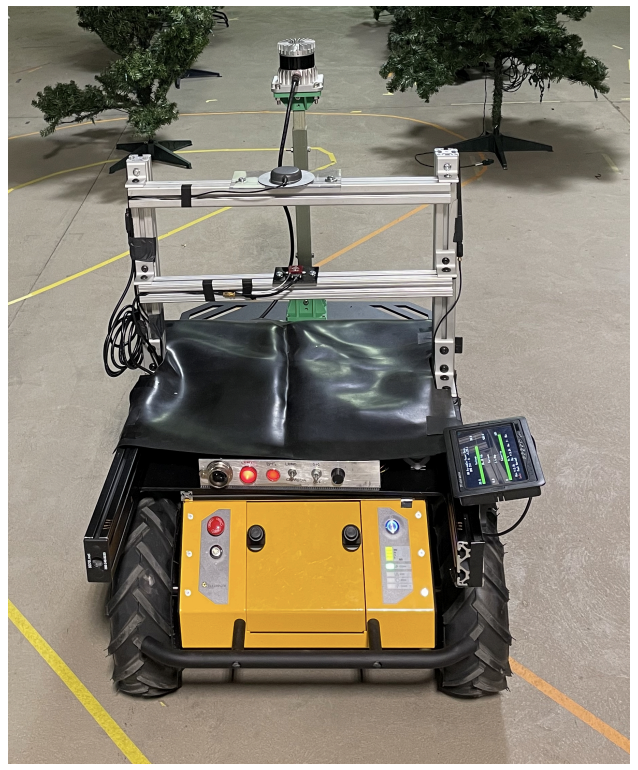
Simulation
——————— Feb. 25 ———————
Vrushali and Simi has developed a basic Gazebo simulation which models the trees in a similar layout to Hale and Hines Nursery.
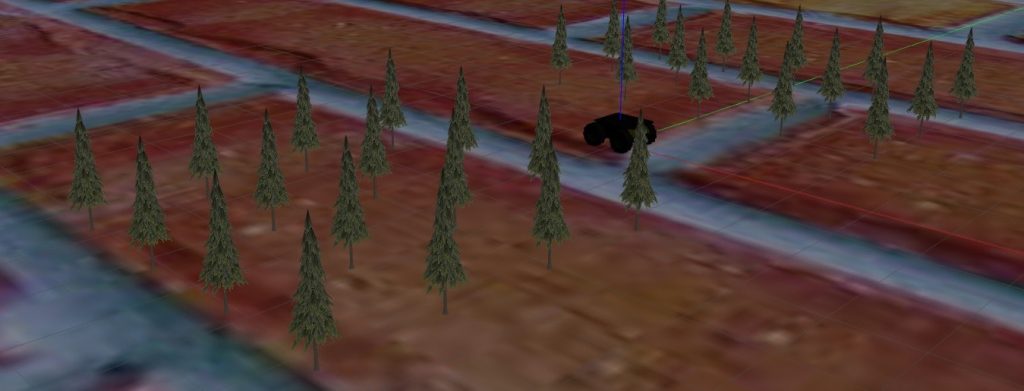
Spraying Mechanism
——————— April. 8 ———————
Suraj built a CAD model for the sprayer. The video below shows the sprayer’s passive 2 degree of freedom, i.e., when running into the obstacles, the sprayer is flexible and compliant.
——————— Feb. 25 ———————
Our collaborator and sponsor, Hale and Hines Nursery has fabricated a custom spraying mechanism for our robot. This mechanism consists of three flippers with an atomizer motor each that allows them to spray a fine mist of herbicide. After receiving this mechanism from Terry Hines, we are working on integrating this electronically into our project so we can control the spraying mechanism autonomously. Terry has also sent us a tank and pots for testing purposes.
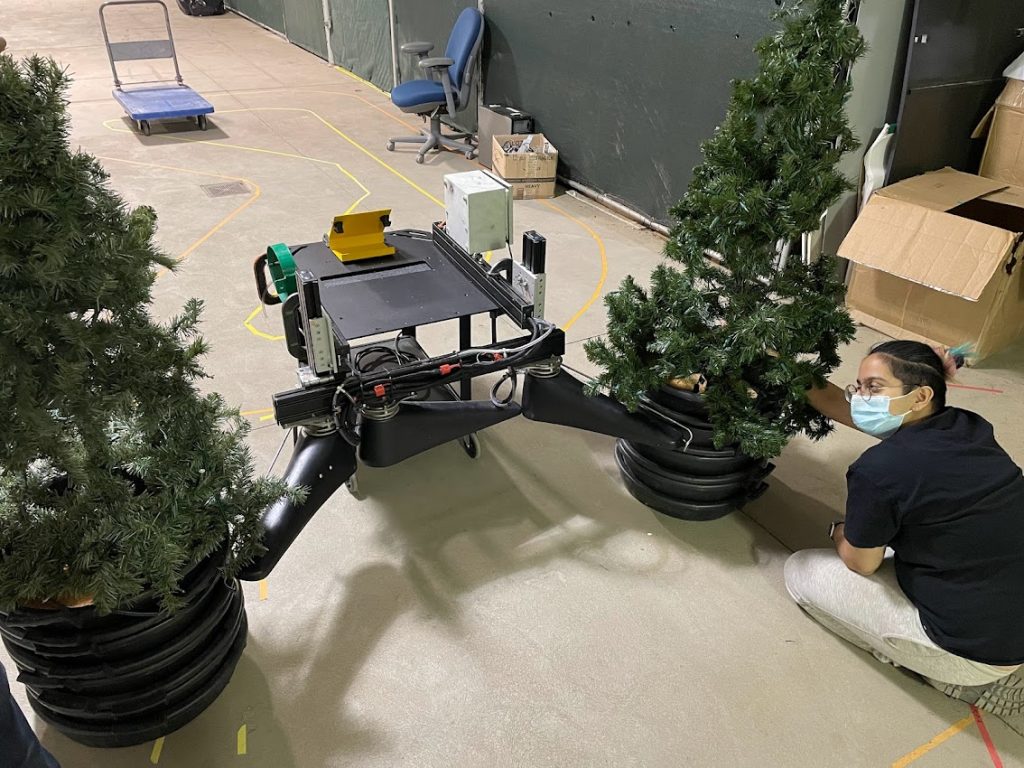
—————— April 20th ——————
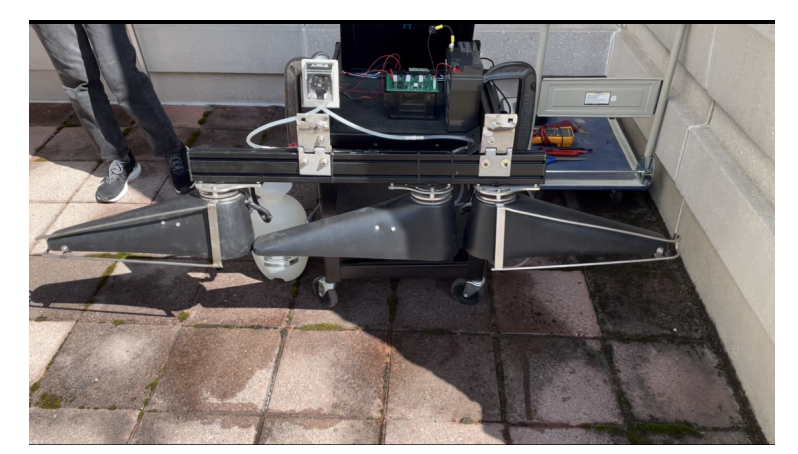
Hardware
——————– April 20th —————-
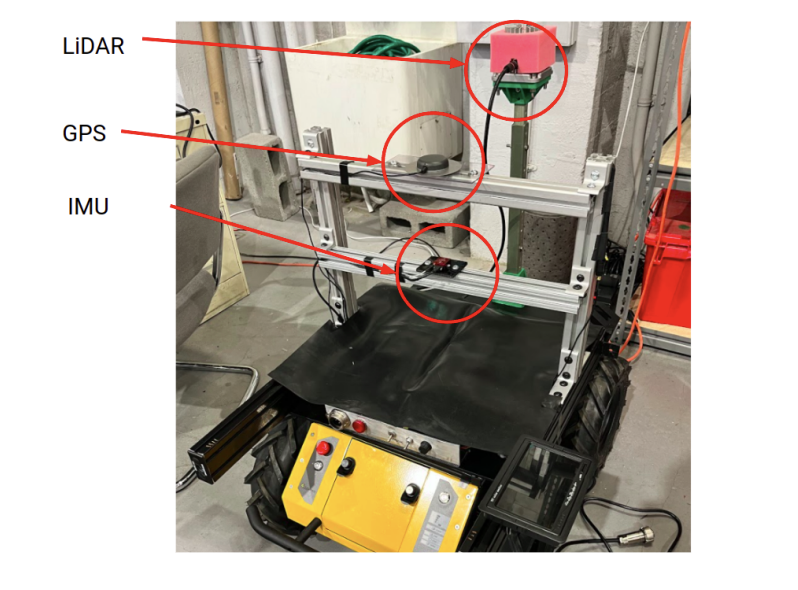
——————– April. 8 ———————
The sensor mounts were fabricated and installed on the robot. The team also cut the new robot’s top plate to create space for the external battery. Now the new battery system extends the runtime from 3 hours to 8 hours.
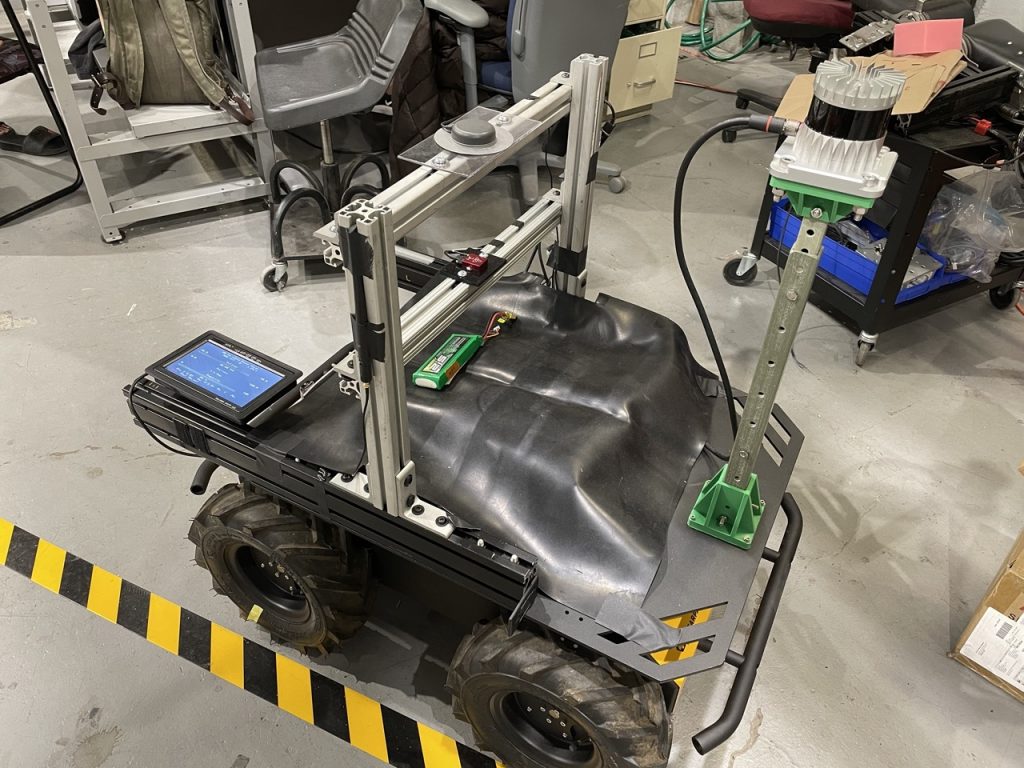
Suraj rendered a nice picture of our robot in the nursery.
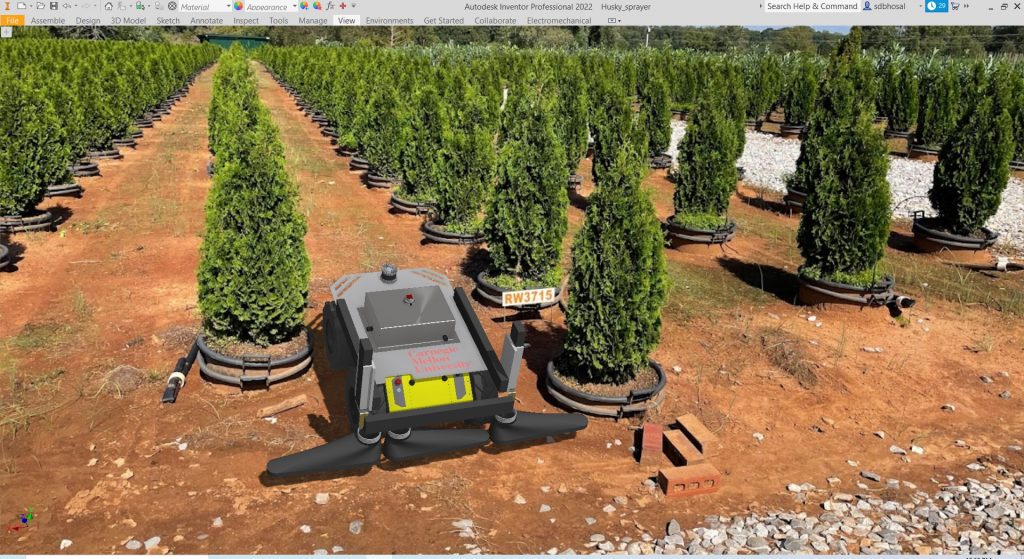
——————— Feb. 25 ———————
Suraj and Simi have been working on the hardware integration of the robot.
Currently, they are fabricating the sensor mounts for LiDAR, GPS and IMU sensors. They are also working on designing an enclosure for the battery and other electronic components that can also be cooled.
Electrical
——————– April. 8 ———————
Vrushali finished designing and implementing the charging system.
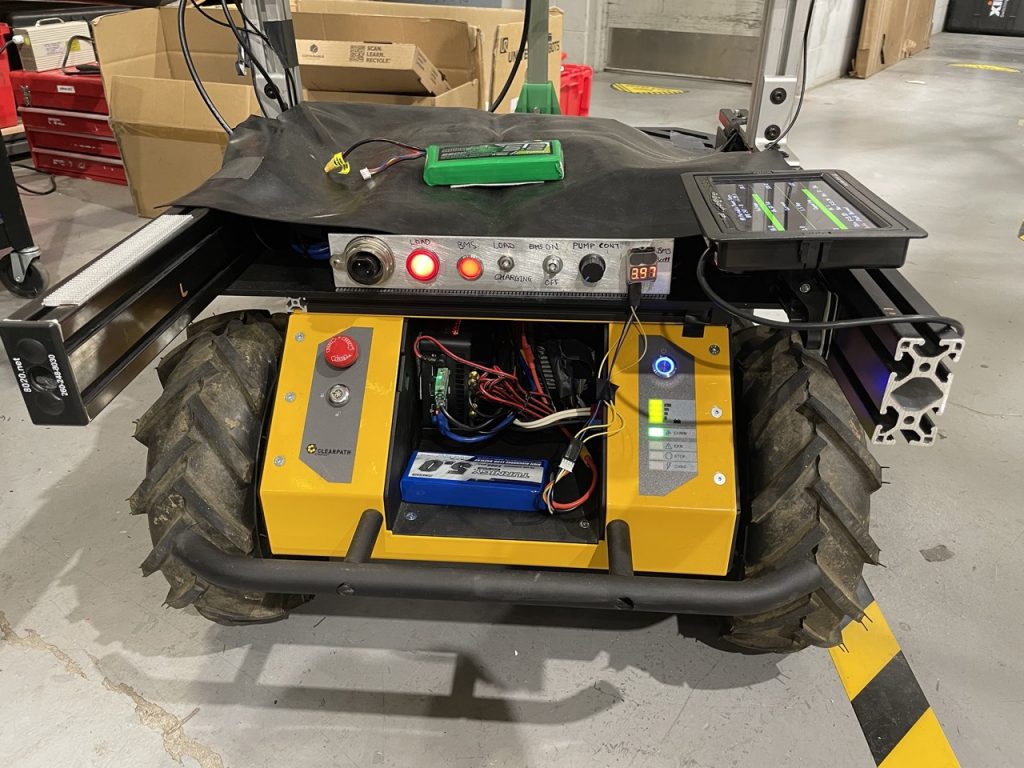
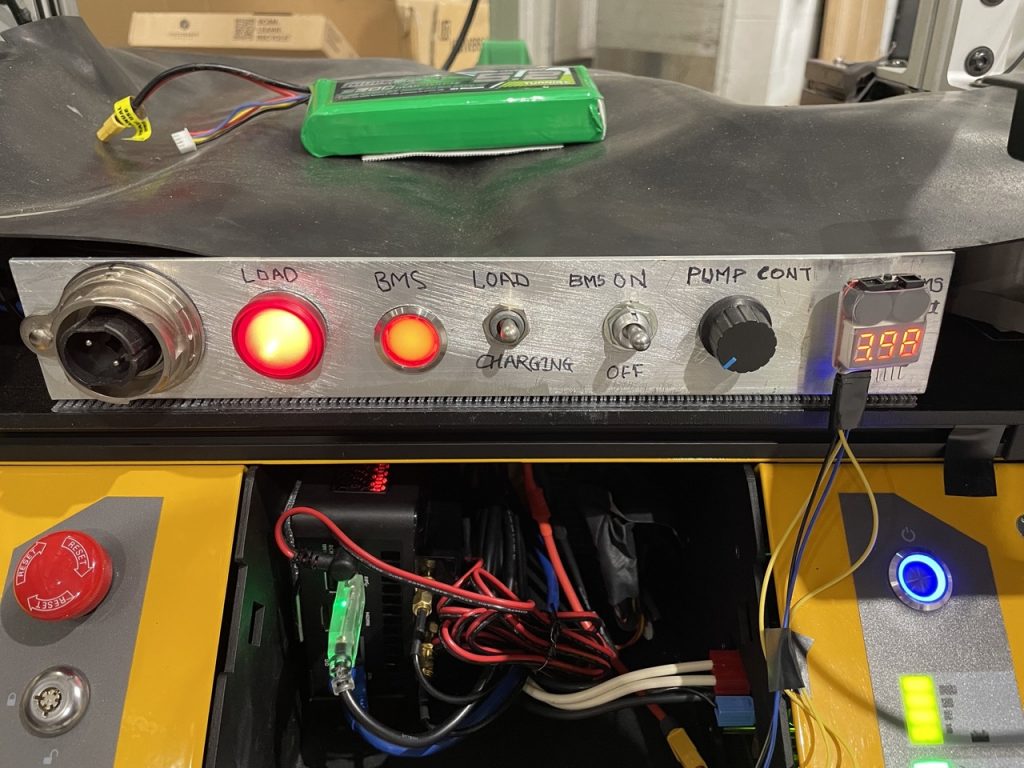
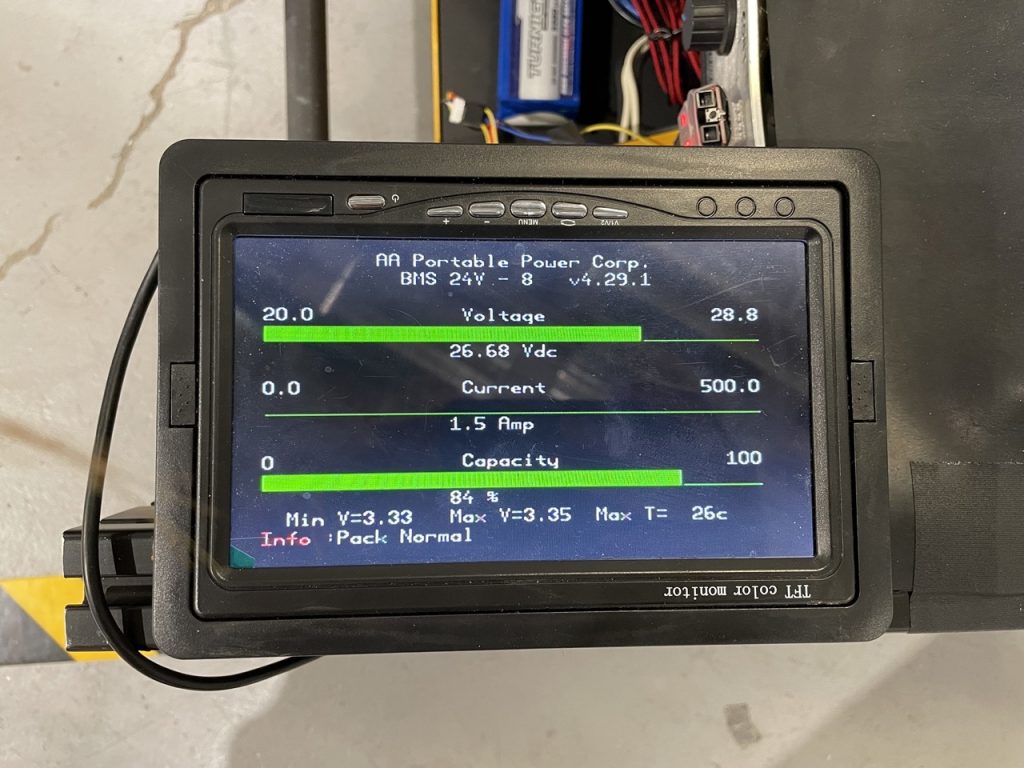
She also designed and soldered the PCB for sprayer control.
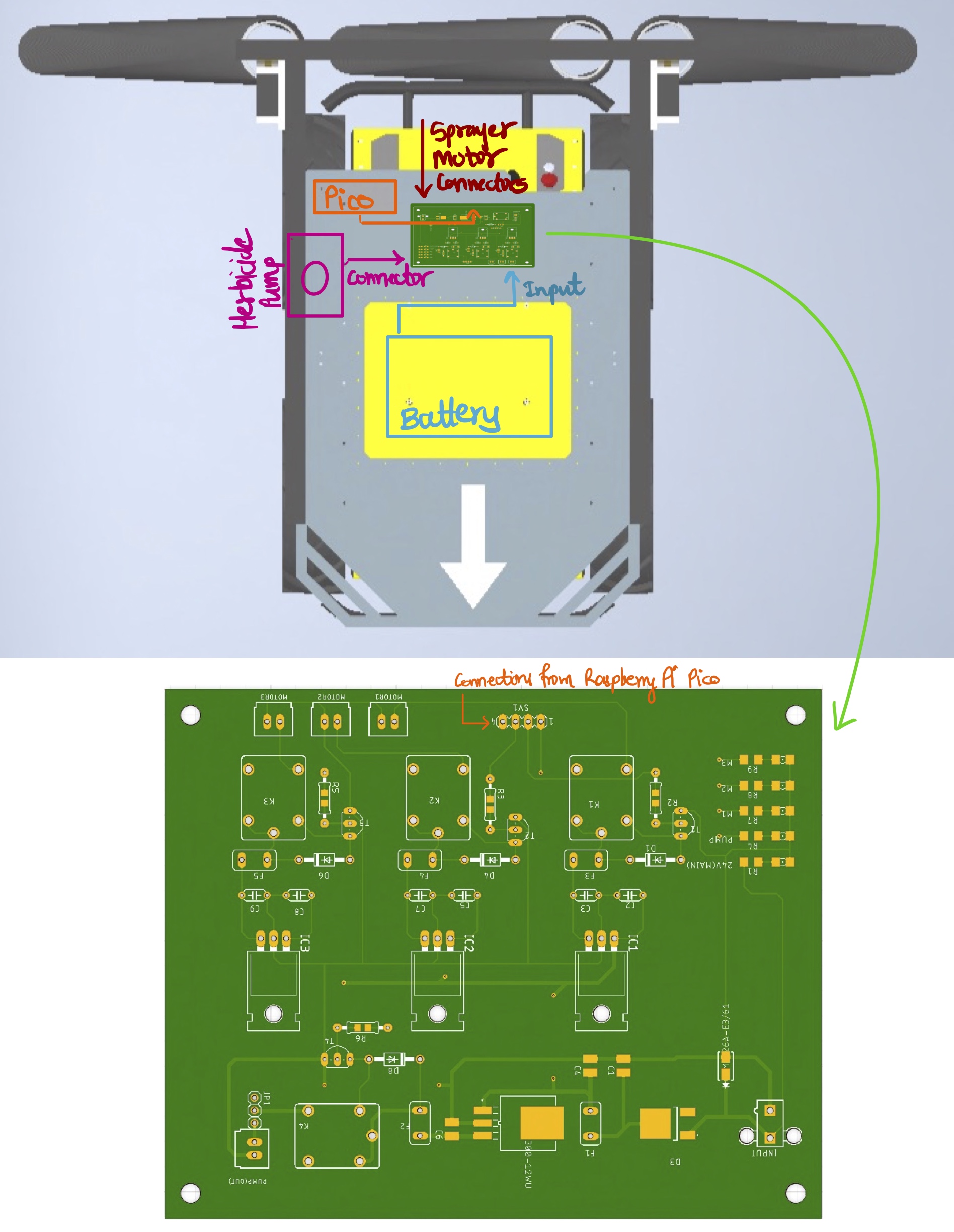
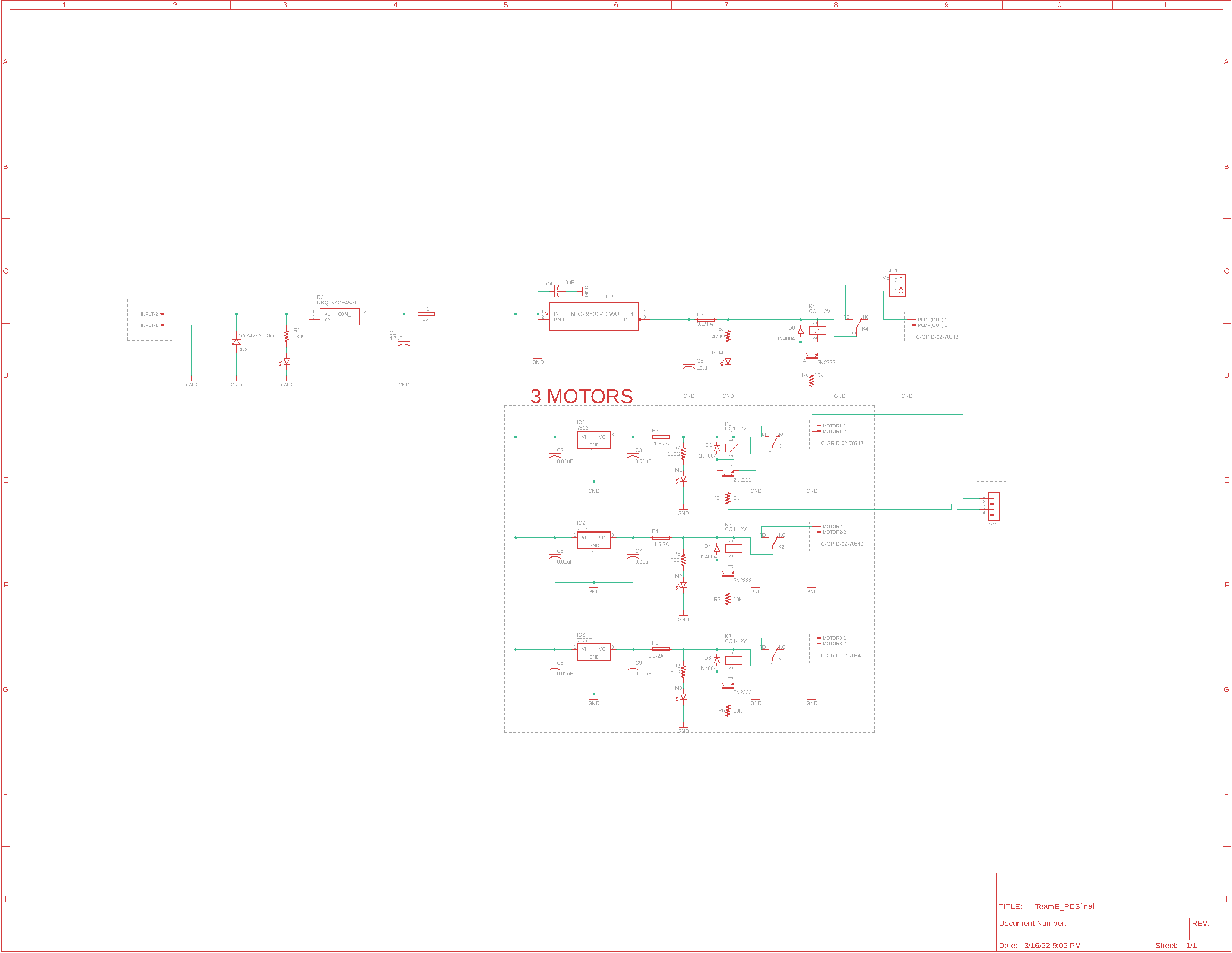
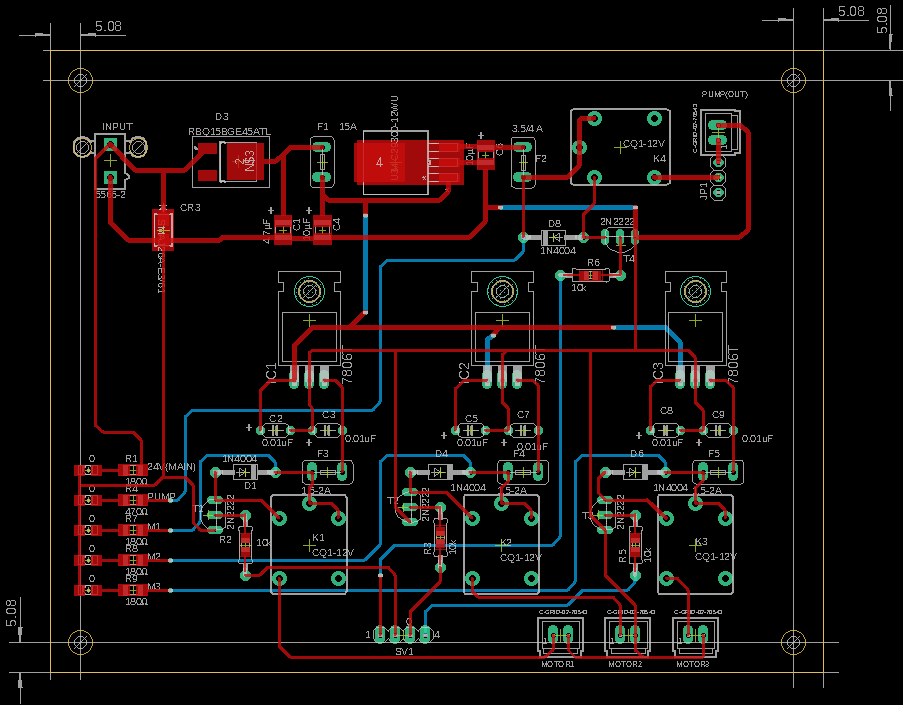
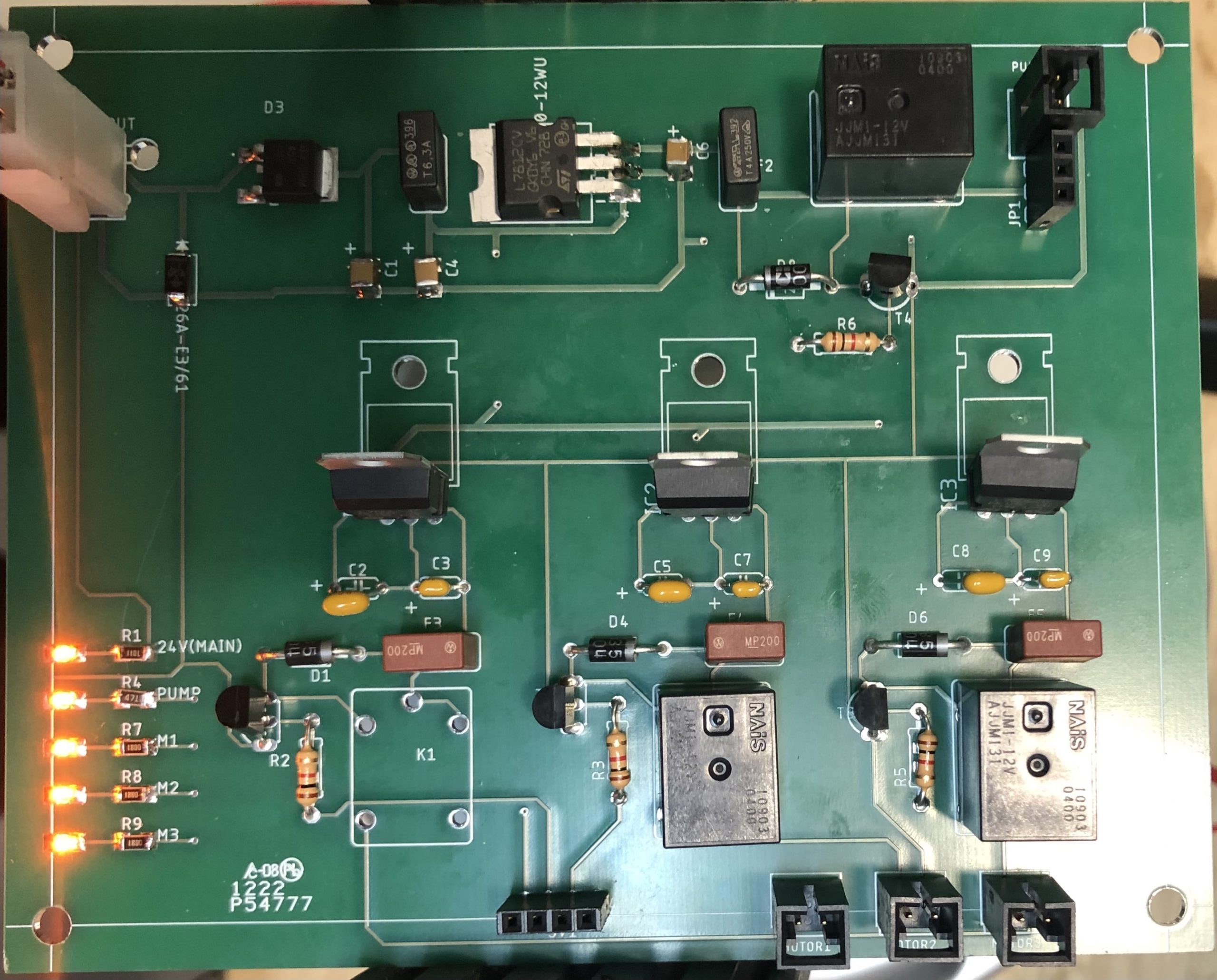
——————— Feb. 25 ———————
Vrushali has integrated a new set of 100Ah batteries with the robot that can provide a run-time of over 6 hours. She is now designing and fabricating a safe and easy-to-use charging system. She is also creating a custom PCB for integrating a micro-controller to digitally control the sprayer and interface with ultrasonic sensor (measure remaining herbicide) and temperature sensor (monitor heat in the enclosure).
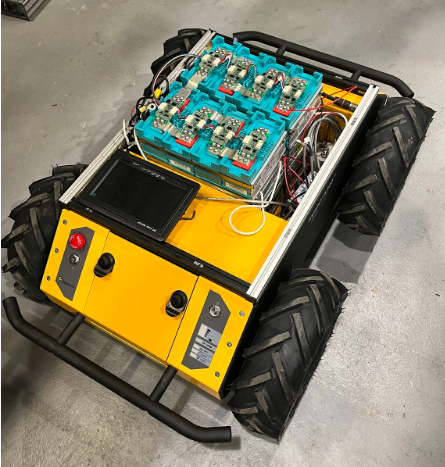
Perception
——————– April 20th —————-
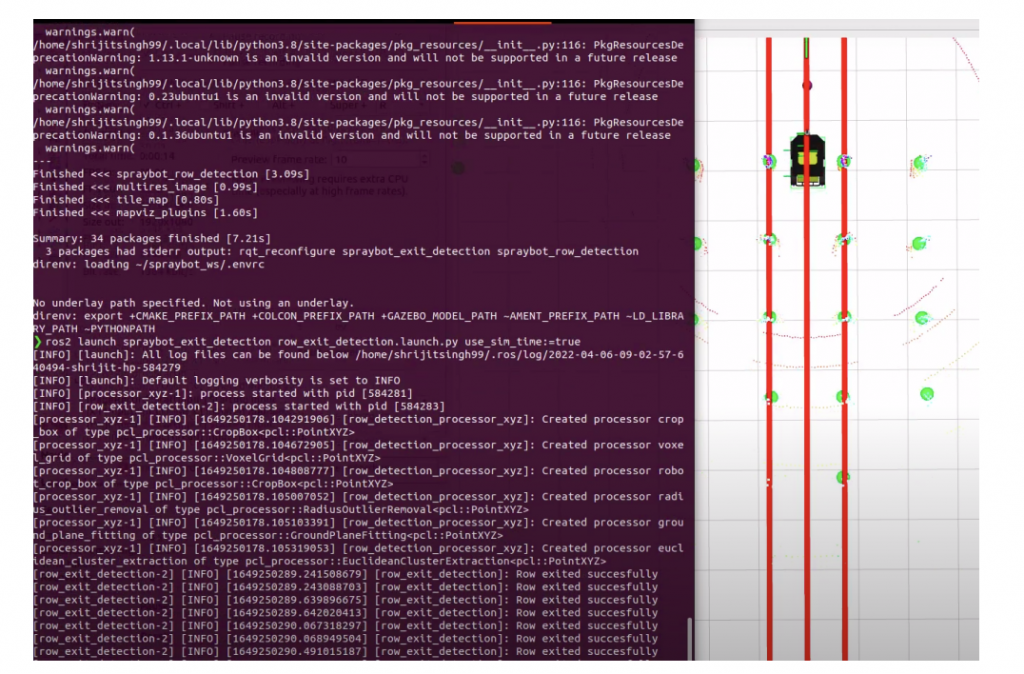
——————– April. 8 ———————
Since the first version of row detection and row following, Simi has optimized the software to be more robust to unexpected rotations in the robot.
Suraj has been working on the row exit detection.
——————— Feb. 25 ———————
Shrijit and Simi have been working on the perception system of the robot.
Shrijit has implemented a pointcloud processing package that provides a lot of flexibility in adding filters and setting re-configurable parameters while being very efficient in processing. You can find a demo of this package here.
Simi has implemented a basic prototype of the row detection package that takes in clusters of trees as an input and provides a waypoint to the navigation system. You can see an example of this here.
Localization
——————– April. 8 ———————
Shrijit verified the GPS with the robot’s odometry.
——————— Feb. 25 ———————
Shrijit has been working on integrating localization on the physical robot. We have done tests to verify the localization software by running the robot at The Cut. In this test we drive the robot in the middle of the road and verify that the GPS estimate stays in the middle of the road as well. You can see the full test here.
Navigation
——————– April. 8 ———————
Shrijit finished and tested the row navigation software. The team made a in-person demo for the guests from Kubota.
——————— Feb. 25 ———————
Shrijit and Vrushali are working on the navigation system. Shrijit has tried to integrate the row detection pipeline into simulation and use it to test navigation. You can see a demo here.
User Interface
——————– April. 8 ———————
Di has completed the frontend, robot client, and basic server code for the web app that monitors robot status and sends simple control commands.
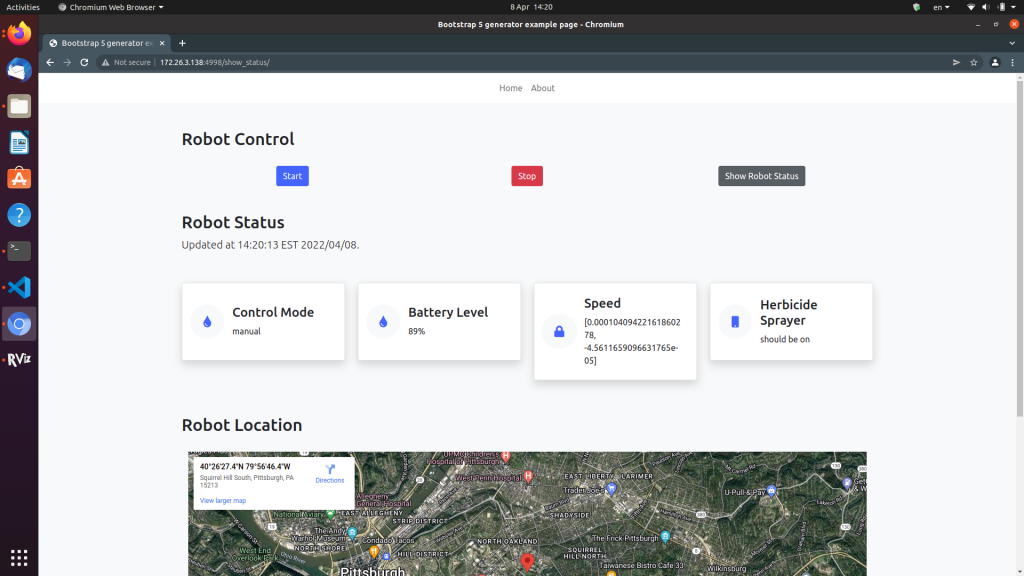
——————— Feb. 25 ———————
Di is collaborating with a team of HCI students to develop the UI for the user to control and monitor the robot.
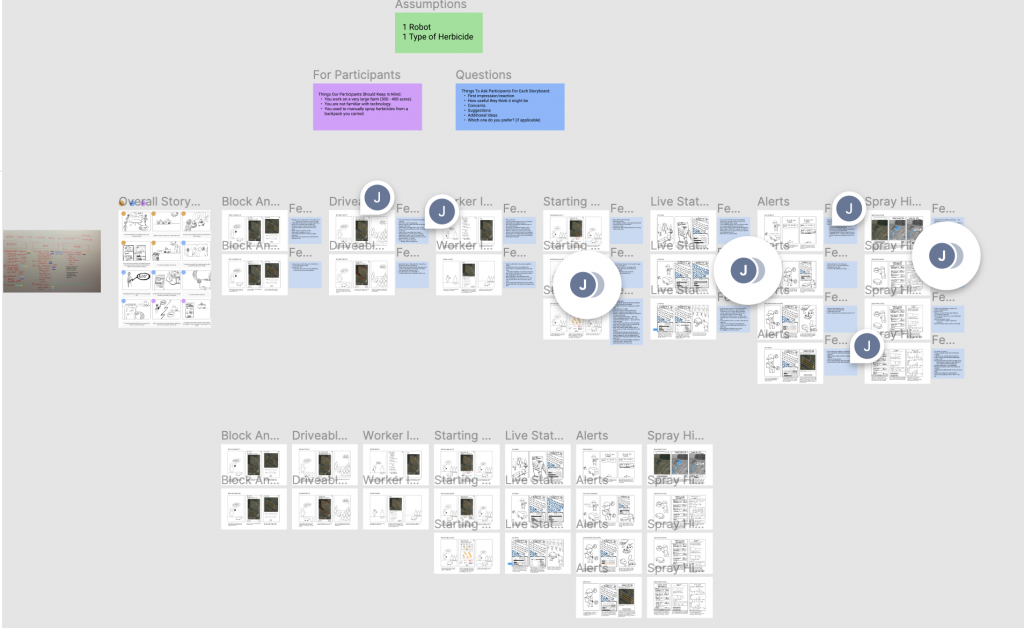
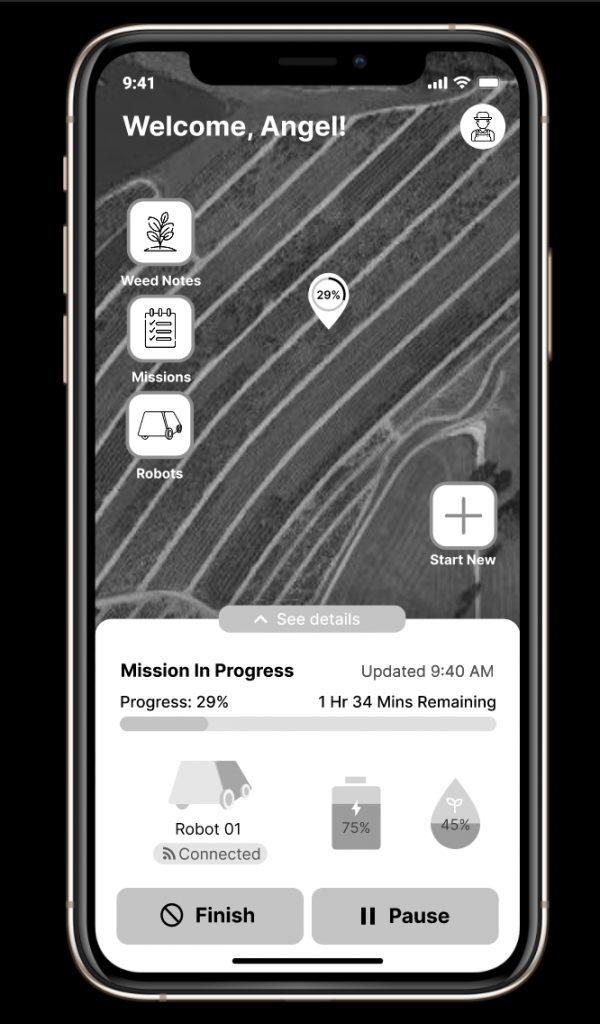