Project Description
The Moon is the key to enabling humanity’s quest to explore the solar system. A lunar presence will act as a gateway to other planets and a research site to develop deep-space technologies and study more about our celestial neighbor. This endeavor requires considerable construction and volumetric site work on the Moon. For this objective, it would be highly impractical to transport raw material in bulk from Earth. Therefore, we will rely on the prevailing materials on the Moon’s surface, specifically the lunar regolith, adopting the concept of In-Situ Resource Utilization (ISRU).
Lunar regolith can be utilized to serve numerous other purposes as well. Studies conducted on the chemical makeup of the regolith suggest that it has elements that can help synthesize propellants and run life support systems. Radiation protection, In-Situ manufacturing, habitat construction, and metal production are also some valuable applications of the material.
Regolith would be required continually in vast supplies to actualize the above-mentioned applications. Having humans excavate and transport these amounts would be perilous, inefficient, and uneconomical. An autonomous solution is ideal, considering the strenuous, mundane, and repetitive nature of the job. A robotic system can be designed to conduct these operations for extended durations efficiently.
The Lunar Autonomous Regolith Excavator (LunAR-X) is a robotic system designed to demonstrate autonomous construction capabilities that are representative of the unprecedented class of volumetric site work required for future lunar establishments.
Use Case
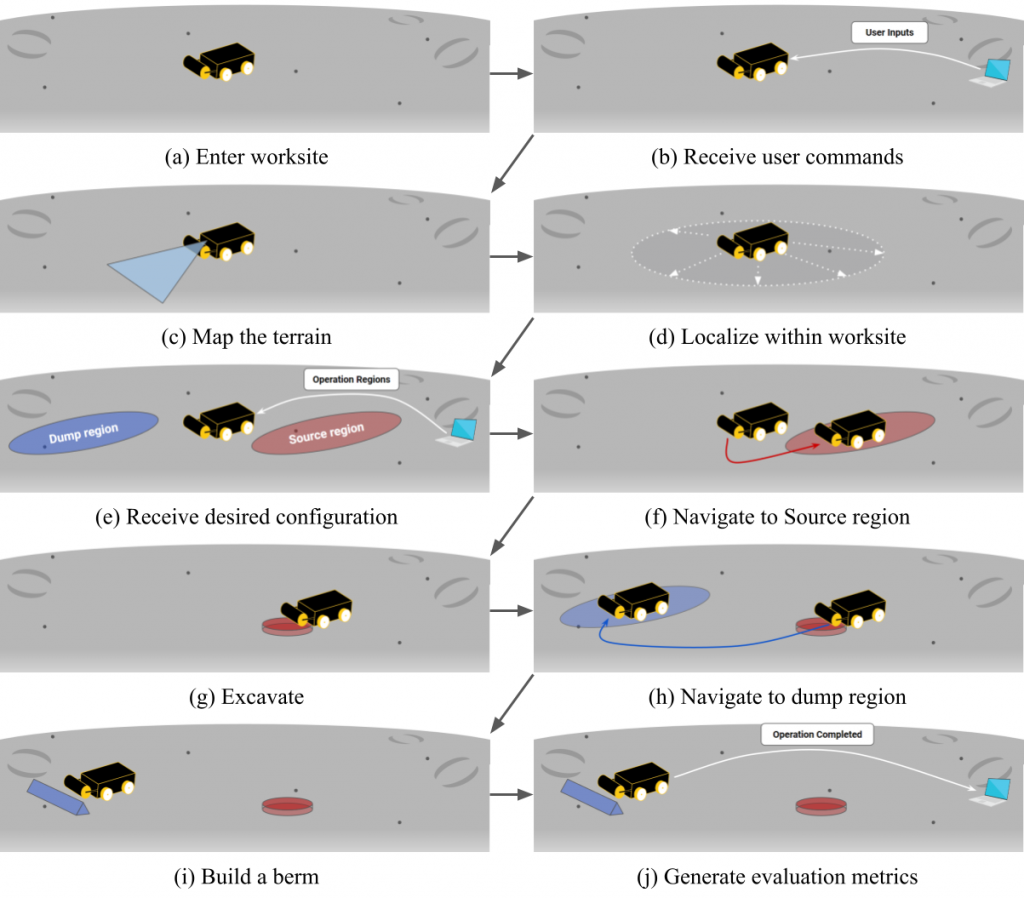
The process begins when the system arrives at the smoothly graded worksite (Fig. 1a) and receives a user command to start autonomous operations (Fig. 1b). The system then constructs a map of the worksite terrain and topography (Fig. 1c), using this map to localize itself within the worksite (Fig. 1d).
Once the mapping is complete, the system will report the map to the user and receive the desired worksite configuration. This configuration describes the shape of the berm that the user wants to build, as well as the operating regions for excavation and dumping (Fig. 1e). With this information, the system can plan the required operations and begin executing them.
The first step in the excavation process is for the system to navigate to the source region (Fig. 1f), where it will begin excavating material (Fig. 1g). This material will be transported to the dump/build region (Fig. 1h), where it will be used to construct the berm (Fig. 1i). This cycle of excavation, transportation, and dumping will be repeated until the desired berm configuration is achieved.
The excavation-transportation-dumping cycle will continue until the desired berm configuration is achieved. Throughout this process, the system will be equipped to assess and re-plan actions if necessary. This will be done using sensor feedback and information about the status of the operation, allowing the system to adapt to changing conditions and continue working efficiently.
The terrain/worksite map will also be updated frequently to assist with navigation and to provide the user with a visualization of progress. This will ensure that the system always has accurate and up-to-date information about the worksite, allowing it to navigate and operate effectively.
Once the berm has been built, the system will generate evaluation metrics and report them back to the user (Fig. 1j). These metrics will provide important information about the performance of the system and the quality of the berm that was constructed. This information will be valuable for evaluating the effectiveness of the LunAR-X system and making any necessary improvements.