Weed Detection and Localization Subsystem
The subsystem uses front, left, and right stereo camera pairs to detect weeds and calculate their position in the world frame. The cameras, calibrated and fixed rigidly, capture synchronized images processed by an onboard Jetson Xavier processor. The weed detection utilizes the ORB algorithm for keypoint detection and stereo triangulation, integrated with the moss© system for accurate world-frame localization. NIR data is used for manipulator-frame output, with NDVI-based segmentation and agglomerative clustering to localize weeds relative to the manipulator.
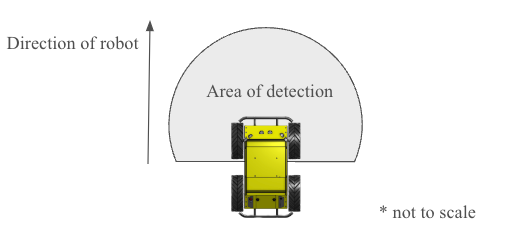
Visual inputs coupled with advanced processing ensure high precision and recall in weed detection. The choice of ORB and NIR technologies is due to their proven effectiveness in similar applications. Alternative methods like direct LiDAR localization were considered but not chosen due to the complexity and cost.
Weeding Manipulator Subsystem
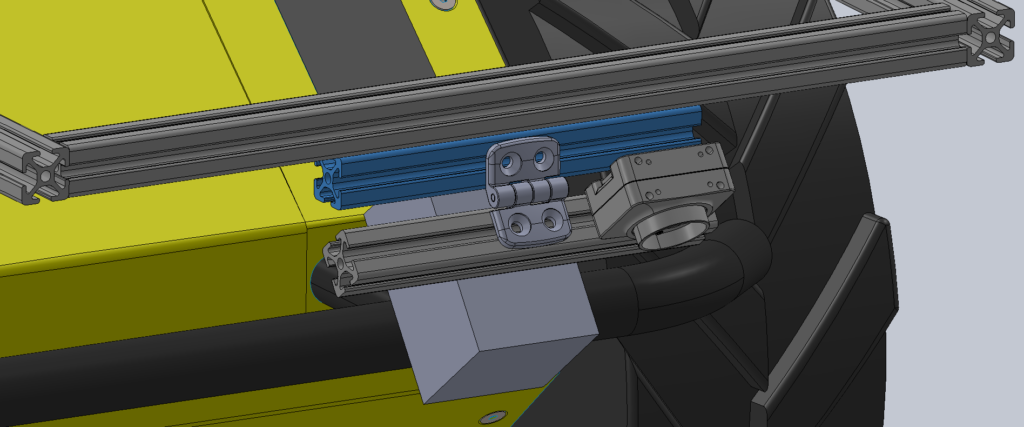
Mounted on a simple aluminum frame, the subsystem features a lead screw and sliding carriage mechanism driven by a stepper motor for linear motion. A hinge and winch servo enable rotation, with the end effector mount designed for easy attachment of tools.
The standardized construction allows for easy iteration and adjustment. The design was preferred over more complex articulations for its simplicity and reliability. Other designs with more degrees of freedom were considered but discarded due to increased complexity and reduced robustness.
Weeding Mechanism
The mechanism will be capable of both chemical spraying and laser weeding, with designs allowing for easy interchangeability. The spraying system uses a peristaltic pump and atomizing nozzle, while the laser system involves a custom PCB and diode laser with heatsink.
The dual-solution approach allows for flexibility and adaptability to different weeding scenarios. Precision spraying offers simplicity, whereas laser weeding provides an environmentally friendly solution. The trade study led to this dual approach over singular methods to capitalize on the strengths of both systems.
Sprayer Mechanism
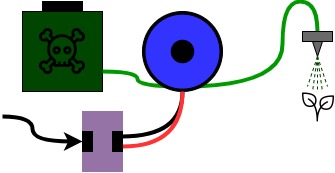
Utilizes a pre-existing design, incorporating a peristaltic pump to move herbicide from a reservoir through an atomizing nozzle directed at the weeds, controlled by a PCB.
The use of a pre-existing sprayer design leverages tested technology and simplifies integration. This was chosen over developing a new system from scratch to save time and resources, given the proven efficacy of the existing design.
Laser Mechanism
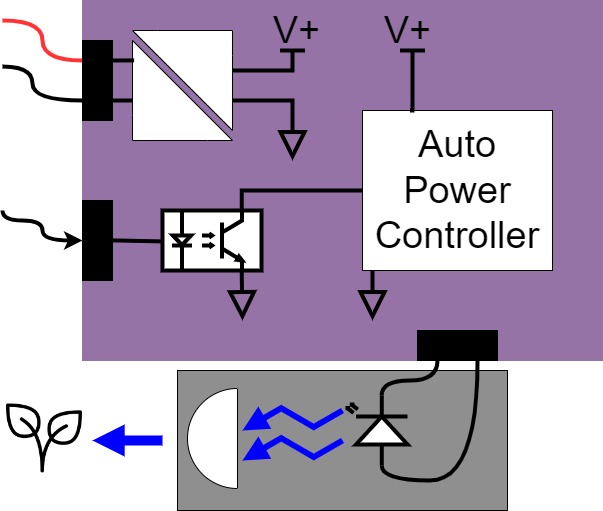
The concept includes a custom PCB to operate a diode laser, with optics and diode mounted in a heatsink. An off-the-shelf laser diode package, like the Snapmaker, offers an alternative with a higher power output.
The internally developed diode laser system presents a cost-effective solution with sufficient flexibility for integration. Off-the-shelf systems, while more expensive and complex to integrate, provide an alternative if the custom solution doesn’t meet performance requirements. Helium-Cadmium Lasers were also considered for their power and compactness but are costlier than diode systems.
Base Brain Integration
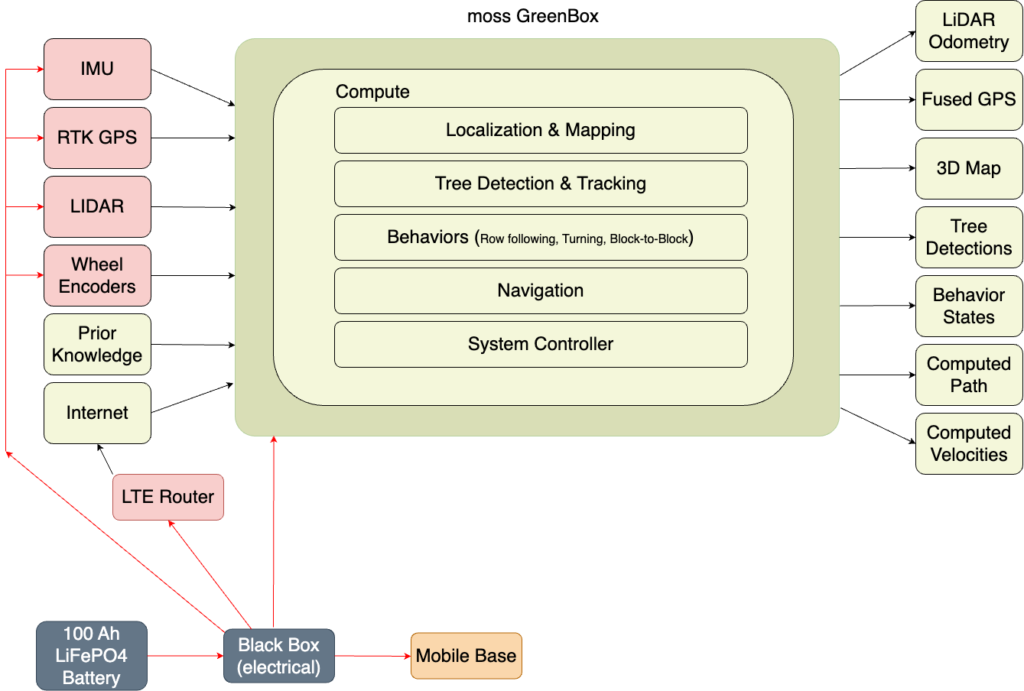
The Base Brain subsystem functions as the central integration point for the autonomous weeding robot, interfacing with the moss© system. It is tasked with reporting weed locations, modifying the robot’s velocity for precise weeding, and activating the weeding mechanism. Communication with moss© is facilitated through ROS message-passing. It also manages the trajectory by slowing down when approaching a weed, stopping during neutralization, and resuming post-weed removal.
This integration is essential for coordinating the robot’s various sensors and actuators to perform its weeding tasks effectively. Using ROS allows for a modular, flexible approach, which can be critical when dealing with real-time robotic operations. Alternative communication protocols were considered but ROS was selected for its widespread adoption and robust support in robotic applications.