After initial brainstorming, we came up with the concept drawing shown in Figure 1. The initial concept shows a fully enclosed kiosk, including a door for the user to access the assembly area. Note that the layout of the bins is different than the eventual design, due to limitations on the Franka Arm’s usable workspace
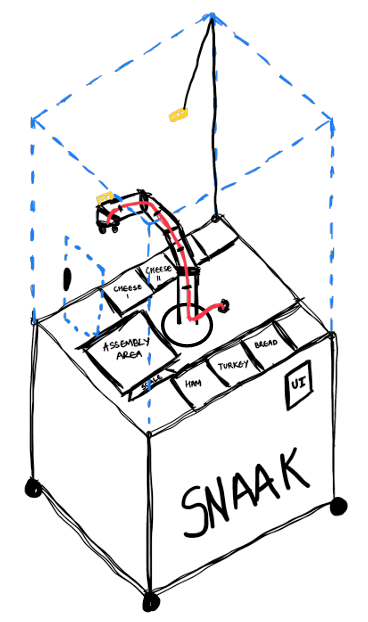
Kiosk
Before settling on the final design, we had several ideas on how to properly construct the workspace. Initially, we planned to fully enclose the workspace with extruded aluminum, and have the workspace be at the same level of the base of the arm. A rendering of this design is shown in Figure 2. However, this design was not optimal, as keeping the workspace at the same level of the base of the arm would greatly reduce the flexibility of arm movements near the workspace as compared to a workspace near the height of the elbow joint of the arm.
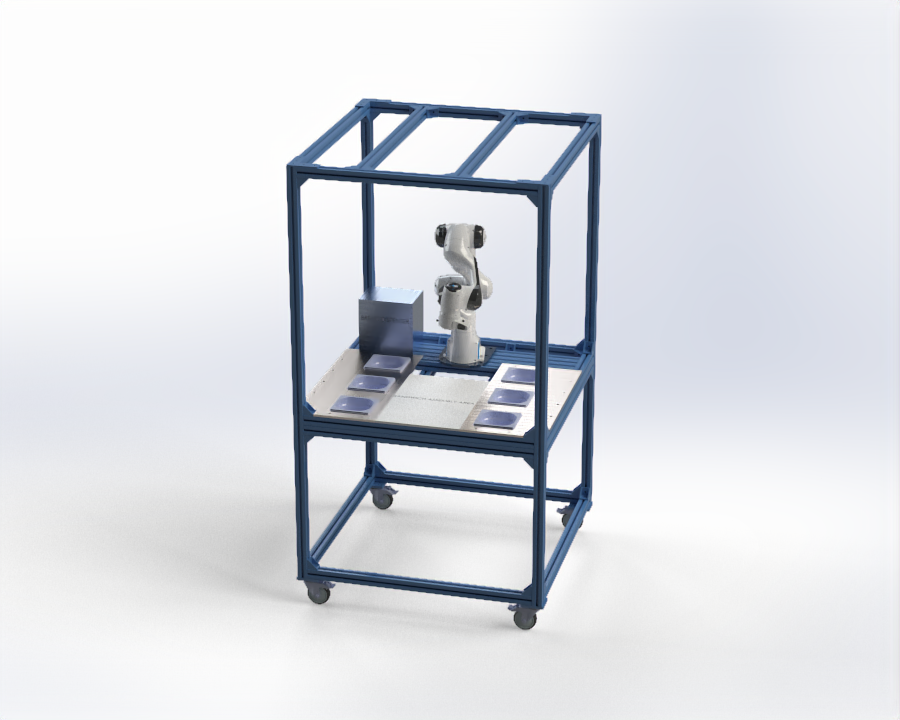
We also decided initially to purchase a suction system from Festo. This system could produce enormous pressure. Figure 3 shows a flowchart of what that system looked like. We did purchase and assemble the system but eventually moved away from it as it could not pick up bread.

Manipulation
After initially planning on using a pneumatic system to pick up bread, we realized that the low-flow system we had purchased was not able to properly pick up the porous bread. As an alternative, we came up with a solution using acrylic “plates”, with bread rested on top to pick up the bread. To place, we would slide the bread of the plate, before placing the plate to the side. A sketch of this concept is shown in Figure 4.
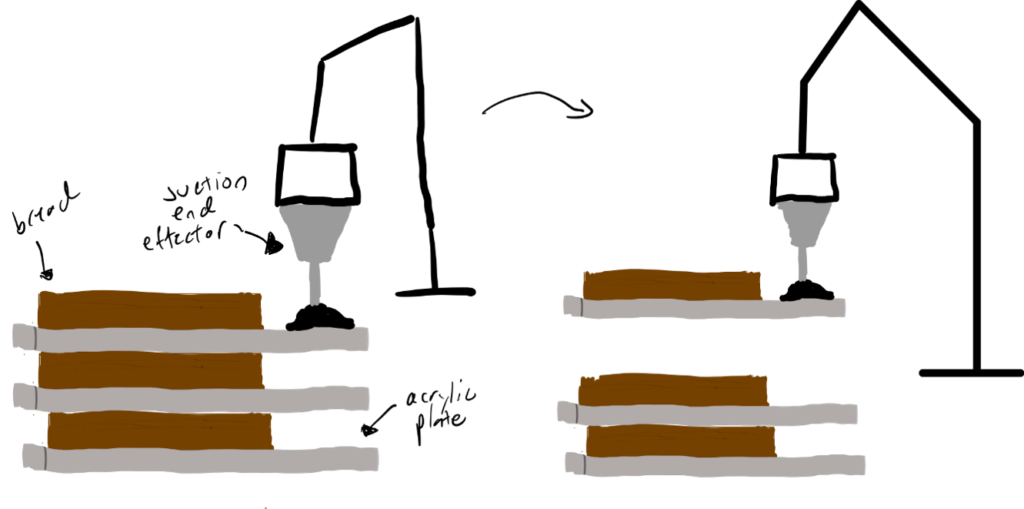
We did eventually develop this method for pickup as part of our risk management strategy while we waited for the high-flow suction system. However, upon successful integration of the new system, this concept was shelved.