ID | Requirement | Class | Description |
FR.01 | Identify Target Peppers | Mandatory | The system should be able to detect green pepper locations and pose on the plants |
FR.02 | Localize and Prioritize Peppers | Mandatory | Based on the location of the peppers the system should be able to deduce the proximity and prioritize the task order for them |
FR.03 | Plan to reach for peppers | Mandatory | After finding the pose, the arms need to plan trajectories to reach the pepper while ensuring that the two arms don’t collide |
FR.04 | Grasp and Cut Green Peppers | Mandatory | Once the end effectors reach, they should grasp the pepper with the gripper and cut the pepper with the cutter |
FR.05 | Store Harvested Green Peppers in Bin | Mandatory | Once the pepper is cut, the system should transport it to the storage bin |
FR.06 | Adapt user inputs to Teleoperation Output Movements | Desirable | The system should produce precise outputs that correspond to the teleop inputs from the users |
FR.07 | Communicate with User | Desirable | The system should communicate with the user and interface the functionality while operating |
FR.08 | Minimize Damage to Pepper | Mandatory | The system should ensure that the peppers are undamaged and are safely extracted |
Functional Requirement | ID | Performance Requirement | Class |
Identify, Localize and Prioritize Green Peppers | PR.01 | Detect fully visible Peppers > 70 % of the time | Mandatory |
PR.02 | Produce estimate pose of green pepper and peduncle within 3 cm of ground truth depth and within 2 cm of other coordinates and upto 30 degrees in each rotation axis | Mandatory | |
Plan Movements | PR.03 | Plan paths that avoid collision with robot itself 95% of the time | Mandatory |
PR.04 | Plan paths that deviate no more than 5cm of the target poses | Desirable | |
Harvest Green Pepper | PR.05 | Reach target green peppers >70% of the time | Mandatory |
PR.06 | Cut identified pepper peduncle successfully >60% of the time | Mandatory | |
Store Green Pepper | PR.07 | Place harvested green pepper inside storage container successfully >80% of the time | Mandatory |
Teleoperation | PR.08 | Ensure compliance to user input >90% of the times | Desirable |
Minimize Green Pepper Damage | PR.09 | Avoids deformation and damage to 90% of picked green peppers | Desirable |
Overall Success | PR.10 | Avoid visible damage to harvested green pepper >90% of the time. | Desirable |
PR.11 | Harvest a fully visible green pepper in testbed autonomously within 100 seconds | Desirable |
ID | Requirement | Class | Description | Performance Description |
NFR.01 | Range | Mandatory | Limit overall size such that platform is able to navigate between crop rows | The arm will reach green peppers 70 cm away from the robot base |
NFR.02 | Size | Mandatory | Fit between pepper plant rows in Iowa pepper farm | The arms will be 50 cm apart |
NFR.03 | Weight | Mandatory | Limit weight based on maximum payload of Amiga mobile robot base | The system will have a weight lower than 35 kg |
NFR.04 | Power Consumption | Mandatory | Limit power consumption based on the battery payload of Amiga mobile robot base | The system will have a maximum power consumption of 700W |
NFR.05 | Modularity | Mandatory | The gripper and cutters have a modular design | – |
NFR.06 | Cost | Desirable | Limit costs as to not exceed MRSD budget | The costs in additional parts for the system will not exceed $5,000 |
NFR.07 | Environment | Desirable | The system will operate in weather conditions identical to pepper farms in Iowa | The system will operate in 50° – 90°F, 400 – 100,000 lux ambient daylight illumination, 50-80 % relative humidity |
NFR.08 | Safety | Mandatory | Be safe to operators and bystanders in the surrounding area | VADER will be safe to operators and bystanders in the surrounding area |
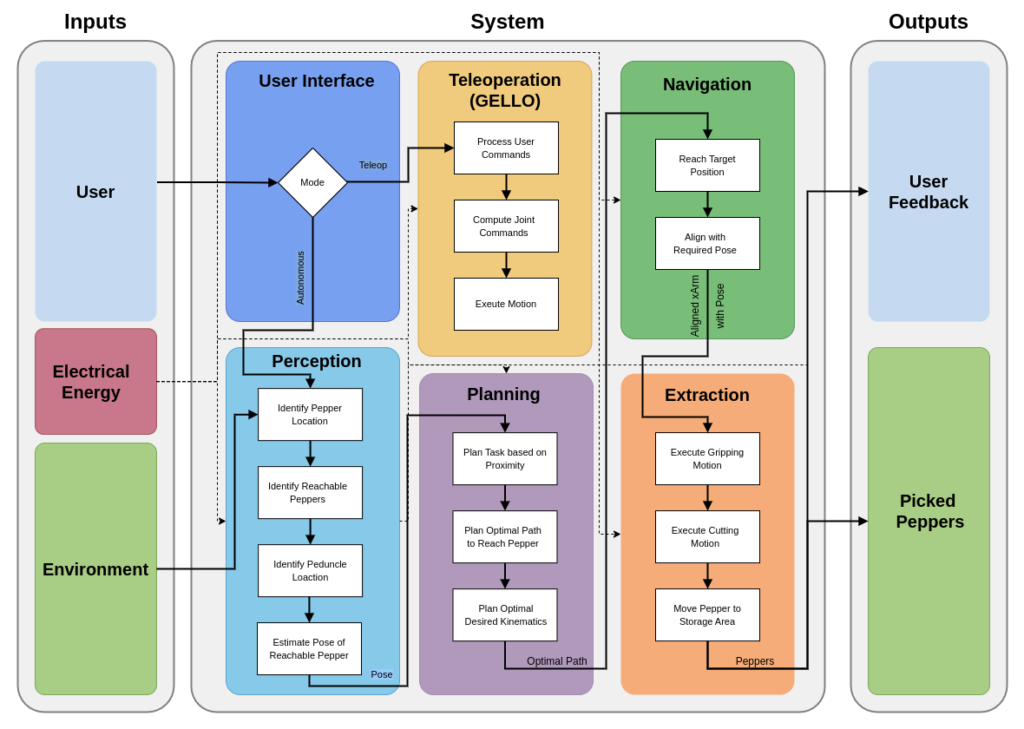
Functional Architecture
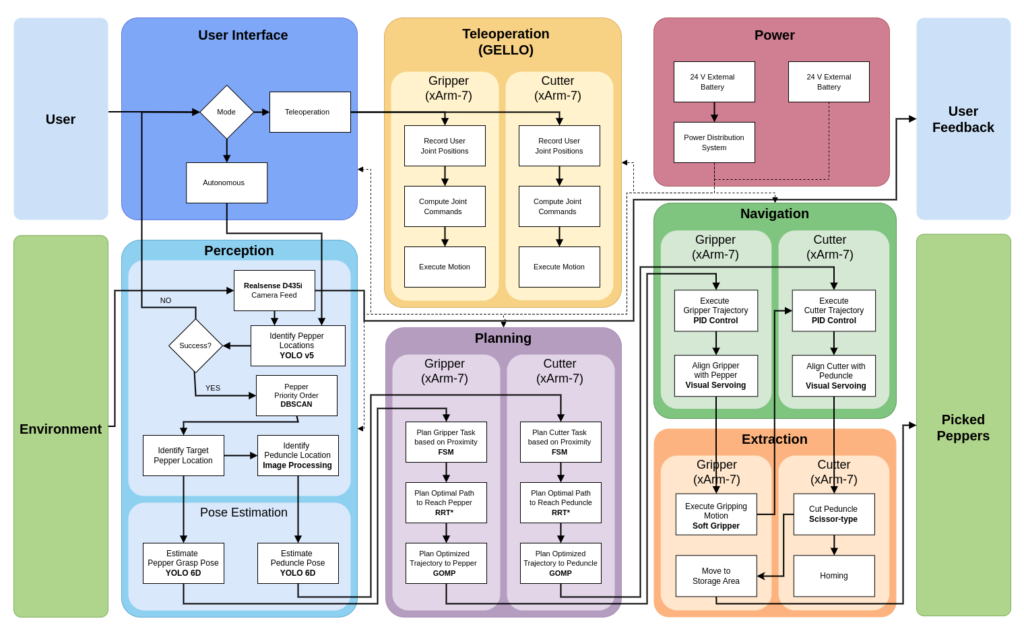
Cyberphysical Architecture
SUBSYSTEM DESCRIPTION
- Perception
The perception system begins with the Realsense D435i camera, which captures the visual information from the environment. Using the YOLOv11-seg detection algorithm, the system identifies the locations of peppers within the camera’s field of view. The DBSCAN clustering algorithm then prioritizes the order in which peppers should be picked. Once a target pepper is identified, a coarse pose estimate is published to the planning team which localizes the arm in the same place as the pepper for a better visual aid. Further a fine pose estimate is computed based on the axis line between the centroid of the fruit and the peduncle. This information further facilitates for further grasping and the peduncle for cutting.
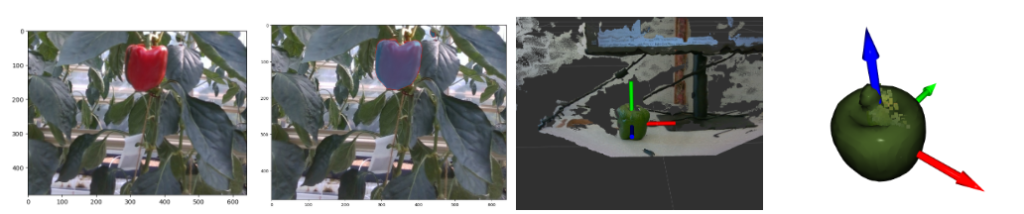
2. Planning and Navigation
The planning subsystem for the Gripper and Cutter (both X-Arms) involves several steps, which are common for the Gripper and Cutter arms. Based on the coarse pose estimate received from the perception node, the gripper arm is moved to the 3D world coordinate using MoveIt! planner and uses a combination of RRT* and Cartesian Planning. Following this, the orientation and exact position of the gripper is refined based on the fine-pose estimate received. The cutter arm follows the same sequence of operation however it is based on the centroid of the peduncle instead of the bell pepper.
3. Extraction
The extraction subsystem handles the actual picking and cutting process. The Gripper arm, equipped with a soft multi-digit gripper, executes the gripping motion to grasp the pepper. The Cutter arm uses a scissor-type mechanism to cut the peduncle, after which, it moves back to the home position. The Gripper arm then drops the harvested pepper into the storage bin and returns to the home position.
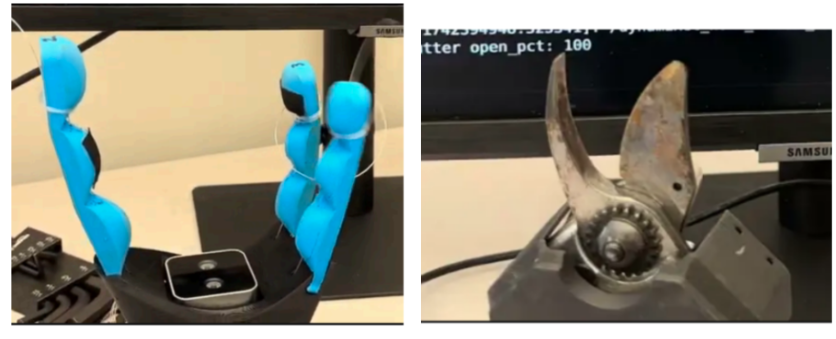
4. Teleoperation
In the Teleoperation mode, two independent robot arms controlled by the user move with the user’s arm motion, recording the user’s joint positions. The recorded positions are translated into executable joint commands, which are then used to synchronously control the motions of the Gripper and Cutter, allowing precise manipulation as directed by the user.
5. Power Distribution
Alongside the main subsystems, we also built a PCB board for power distribution across the end effectors, teleoperation consoles and the amiga platform. The Amiga system delivers a stable 12-volt supply to the board, which then distributes power to the gripper, cutter, and both teleoperation arms. An integrated emergency stop mechanism is included to immediately cut off all incoming power and deactivate the end effectors in the event of a malfunction. The board was successfully tested during the SVD Encore trial, confirming its ability to reliably power all connected components. The PCB steps power down to 5V for the teleoperation consolves and transfers 12V of power to the end effectors.