Problem Description
The warehousing industry faces critical challenges in ensuring the safety and efficiency of operations. With a significant annual rate of injuries (~4.8 per 100 employees) and deaths (~21) in the U.S. alone, warehousing remains a high-risk occupation. The prevalence of low back pain, particularly among young warehouse workers, highlights the physical toll of manual tasks such as tote manipulation, a common activity in warehouse logistics. With the market for warehouse automation, currently valued at $16 billion, projected to grow at a compound annual growth rate (CAGR) of 18.7%, reaching up to $54.53 billion by 2029, there is an increasing demand for innovative solutions for minimizing human warehouse effort.
To address these challenges, the project aims to develop an autonomous humanoid system designed for tote logistics in warehouses. A humanoid form is particularly suited for this scenario due to its inherent design advantages in environments built for human workers. Warehouses are typically structured with human-centric dimensions, such as aisle widths, shelf heights, and ergonomically placed items. A humanoid robot can seamlessly operate in these spaces without the need for significant infrastructure modifications, making it a cost-effective and scalable solution. By leveraging advanced loco-manipulation capabilities, the humanoid will navigate dynamic warehouse environments, perceive and localize targets, and execute tasks like pick-and-place with high precision. The solution prioritizes reliability and safety while ensuring minimal disruption to existing workflows. Performance benchmarks include maintaining locomotion precision, avoiding obstacles, and achieving a high tote manipulation success rate. Furthermore, the system’s potential generalizability opens opportunities for applications beyond warehouse logistics, such as EV charging and Body-in-white (BIW) automobile wire harness installation.
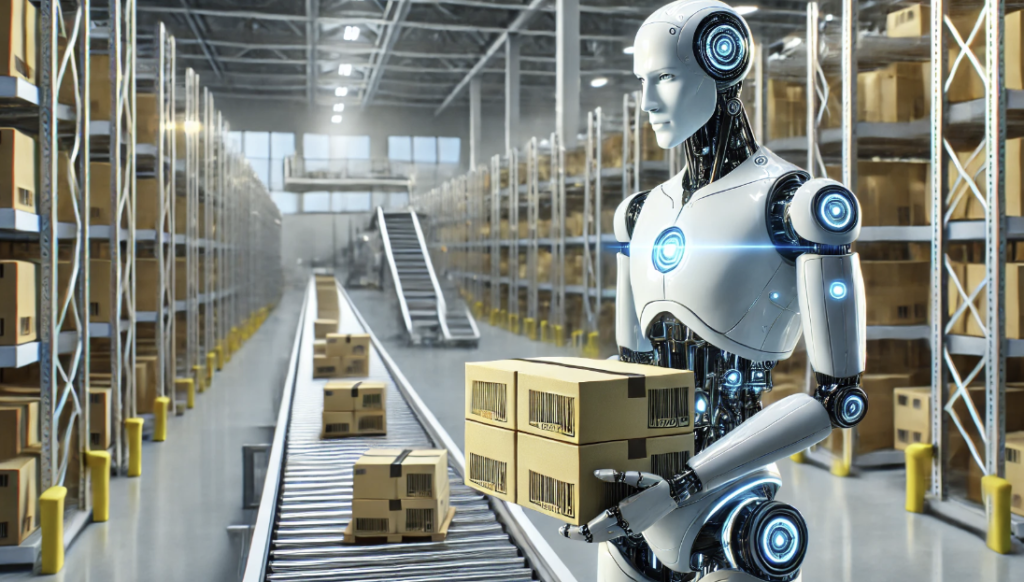
Use Case
Warehouse worker Sam is tasked to move boxes from one conveyor to another in a high-throughput environment. It involves heavy boxes and repetitive bending and lifting, which put significant strain on his lower back. Over time, this manual labor leads to fatigue and increases his risk of injury. The management, aware of the safety concerns and operational inefficiencies, deploys an autonomous humanoid robot to assist Sam and streamline the process.
Scenario:
- Setting: Sam works in a large warehouse with narrow aisles, stacked shelves, and constantly moving conveyors. The workspace is designed with human ergonomics in mind, such as specific aisle widths and shelf placements.
- Actors:
- Sam: Oversees robot operations and provides occasional input, such as troubleshooting or task prioritization.
- Humanoid Robot: Handles the physical task of moving boxes, equipped with precision loco-manipulation and navigation systems.
- Process:
- The robot is programmed via the database of pickup and drop locations with the task of transferring boxes from one conveyor to another.
- The humanoid autonomously navigates the warehouse, avoiding obstacles such as workers, equipment, and other robots.
- Upon reaching the conveyor, the robot identifies a box using its perception system, grips it securely with its manipulators.
- The robot walks to the target conveyor, maintaining stability while carrying the box and avoiding collisions or disruptions in the workflow.
- Once at the destination, the robot precisely places the box on the target conveyor in the preferred orientation. It repeats this process until the task is completed.
- Meanwhile, Sam supervises multiple robots through a centralized interface, ensuring smooth operation and stepping in only if needed.
Outcome:
- The robot reduces Sam’s physical workload, protecting him from injuries like back strain.
- The warehouse achieves a higher throughput, as the robot operates tirelessly and with consistent speed and precision.
- The humanoid seamlessly integrates into the existing workspace, avoiding the need for costly infrastructure changes.
- Sam focuses on higher-value tasks, such as monitoring robot performance or handling exceptions and enhancing productivity.