Problem description
We understand the complexities and challenges of inspecting large, heavy, and intricate components in modern manufacturing. That’s why we’ve developed MAGIC (Multi Agent Geometric Inspection & Classification)—an advanced system designed to revolutionize the way large objects are inspected. MAGIC is a versatile and generalized solution that can handle a wide range of unspecified objects, making it a scalable tool to meet the diverse needs of our clients across various industries.
MAGIC utilizes two advanced robotic arms to seamlessly manipulate and position even the heaviest parts with ease. These robotic arms ensure precise handling, lifting, and rotating of large components, allowing for thorough inspections from every angle. By providing a 360-degree view of the product, MAGIC guarantees comprehensive coverage, eliminating blind spots and human error that can occur with traditional inspection methods. Additionally, MAGIC creates an accurate 3D model of each part by capturing high-resolution images from multiple perspectives, ensuring that every surface and detail is meticulously examined. This 3D model helps to detect even the most subtle flaws, enhancing the precision of the inspection and enabling detailed analysis.
What sets MAGIC apart is its ability to detect defects based on specific criteria set by the customer, from surface imperfections to structural flaws like cracks or scratches. The 3D model generated during inspection offers further insights, enabling comparisons with design specifications to assess the part’s quality with unparalleled accuracy. Beyond just detecting defects, MAGIC collects and organizes critical quality data, providing valuable insights into the production process and helping manufacturers improve overall product quality and efficiency.
By offering an automated, reliable, and thorough inspection process, MAGIC reduces the physical strain of manual inspection while ensuring consistent, repeatable results. With MAGIC, manufacturers can meet higher production standards, minimize costly errors, and maintain a competitive edge in the industry. Rest assured, with MAGIC, every part is inspected with the utmost care and precision.
Use Case
Meet Mike, a quality assurance technician in an automotive factory where he inspects large, complex parts—like engine casings—for surface defects. Handling these parts is tough; making it hard to thoroughly check each one. Manual inspection requires Mike to lift and rotate each part, often with assistance, but the variability and sheer size make it difficult to ensure a complete view. Missed defects lead to costly rework and risks in the field.
Imagine if Mike had an advanced system designed to handle these challenges. Equipped with two robotic arms, this system picks up and manipulates components mid-air. Equipped with a high-resolution inspection camera, the robot captures detailed images from multiple angles. It not only detects defects like dents and scratches but also performs 3D reconstruction to create an accurate model of the sample and generate comprehensive reports on the sample quality.The system senses its environment and plans each coordinated move, avoiding collisions and optimizing inspection routes for higher throughput. With its ability to automatically recover from misalignments and other issues, every inspection is highly repeatable and consistent, covering each surface while minimizing downtime.
By reducing manual labor, ensuring defect-free products, and boosting throughput, Mike’s team can confidently keep up with production demands and meet modern QA standards.
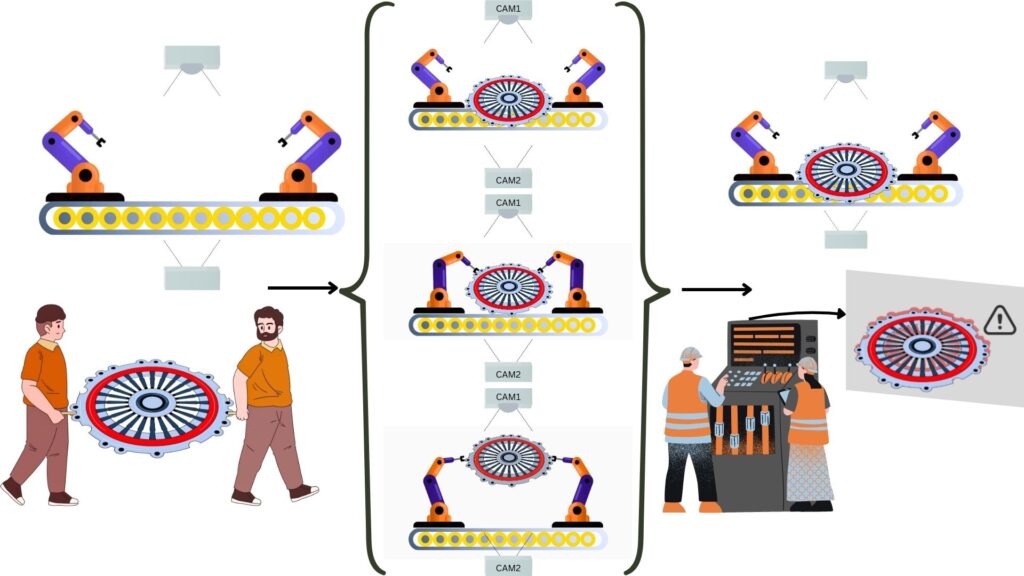