Fall Semester Implementation Details
In the Fall semester we gave a major makeover to our UAV subsystem where we made a moved on from our custom hexacopter platform to the DJI Matrice M210 V2
UAV Implementation Details
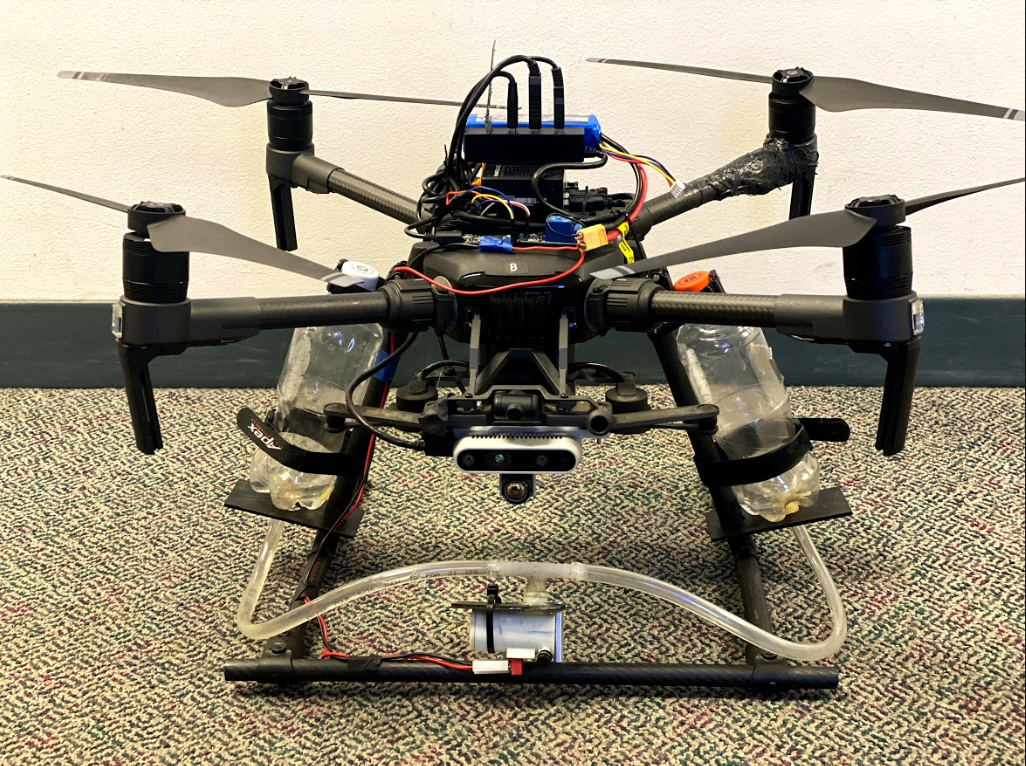
UGV Implementation Details
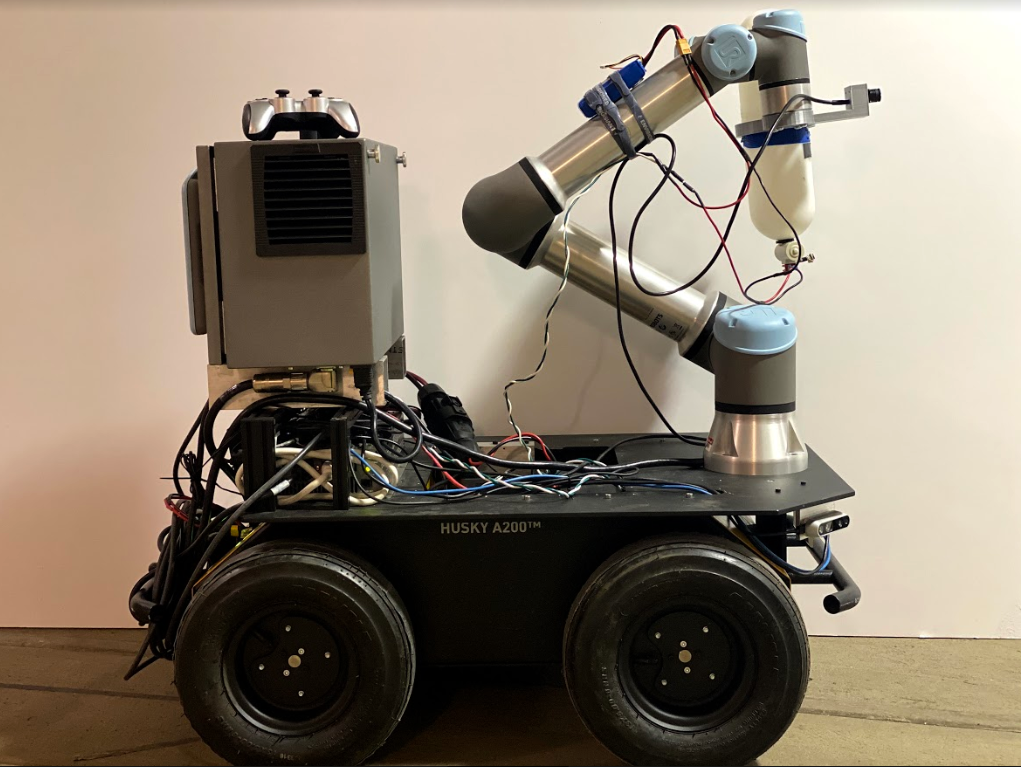
Spring Semester Implementation Details
The hardware subsystem is broken down into two components. A aerial vehicle and a land vehicle.
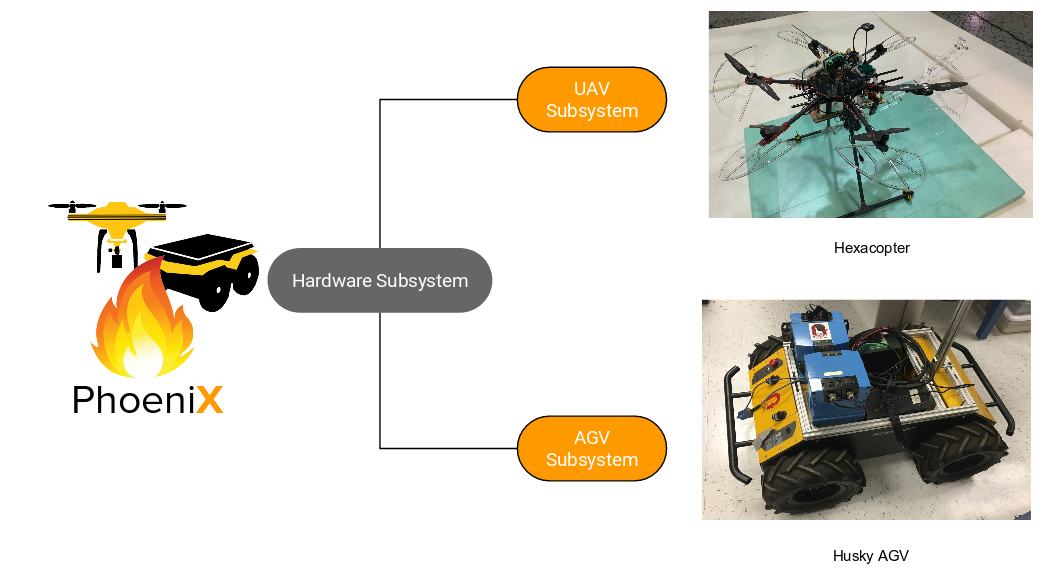
UAV Implementation Details
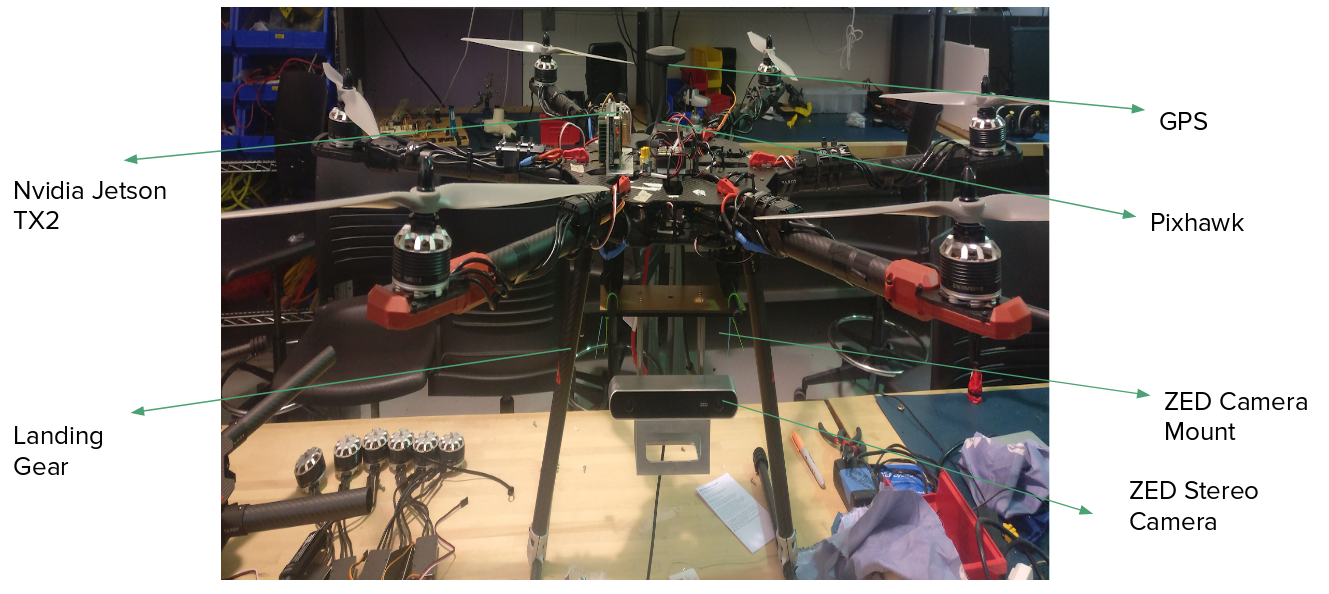
UGV Implementation Details
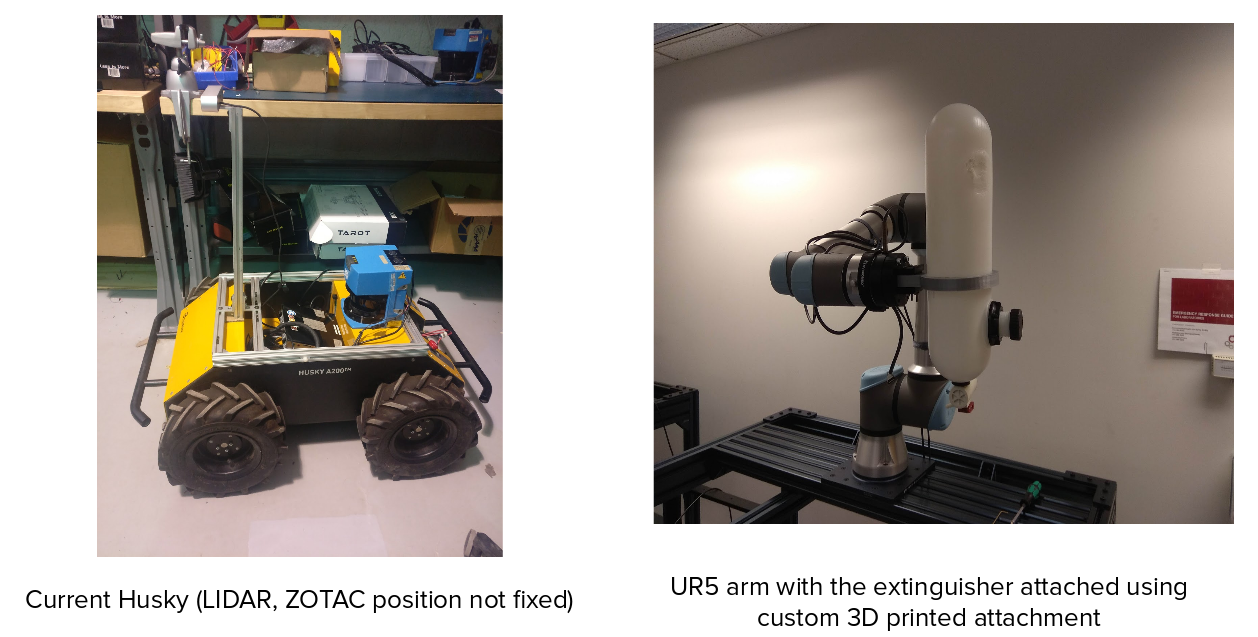
As per MBZIRC size constraints we have also assembled a UAV which meets the current constraints and it will act as a reserve in case some damage happens to our main UAV. The reserve UAV also features the tilted hex design and which can be seen below.
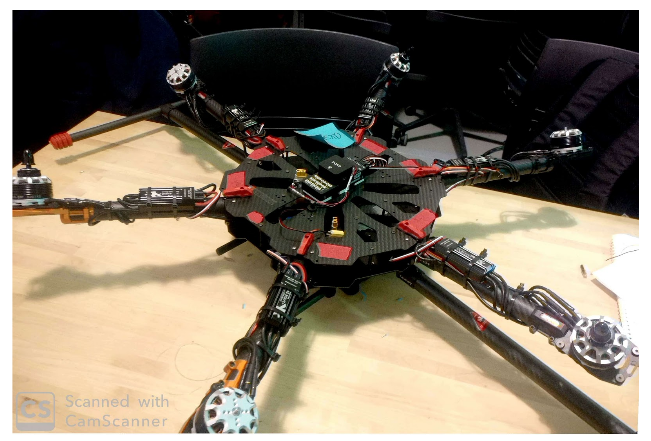
The videos below provide a better sense of understanding of the UAV and UGV system as on April 5, 2019
Video for UAV:PCB for UGV
To power the various components on the UGV we have also designed our custom PCB which is capable of powering our LiDAR, cameras, actuators and also the various other sensors such as GPS and IMU. The schematics and various other files related to this PCB can be found in documents section here
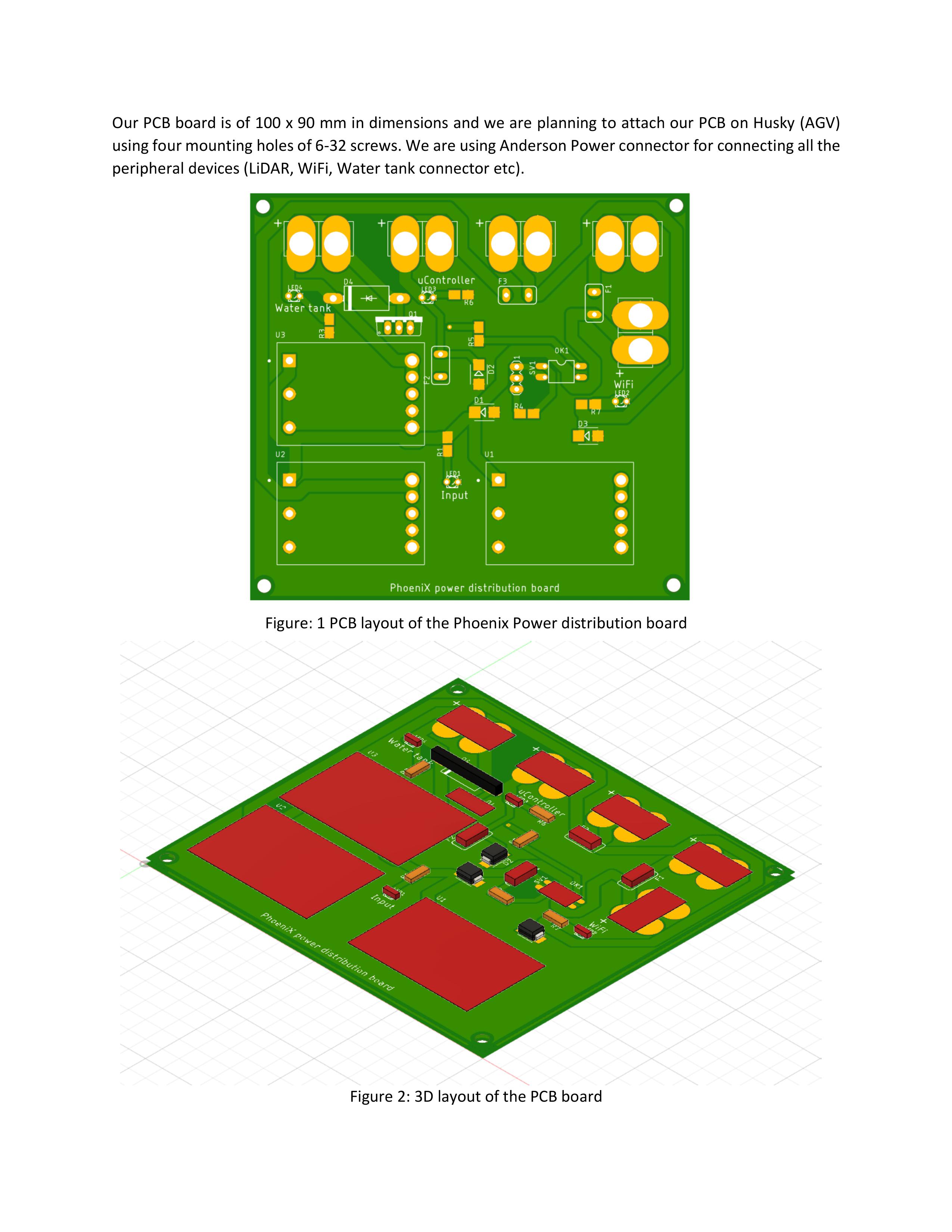
The PCB schematic highlights the various important aspects of the electrical subsystem of the AGV.
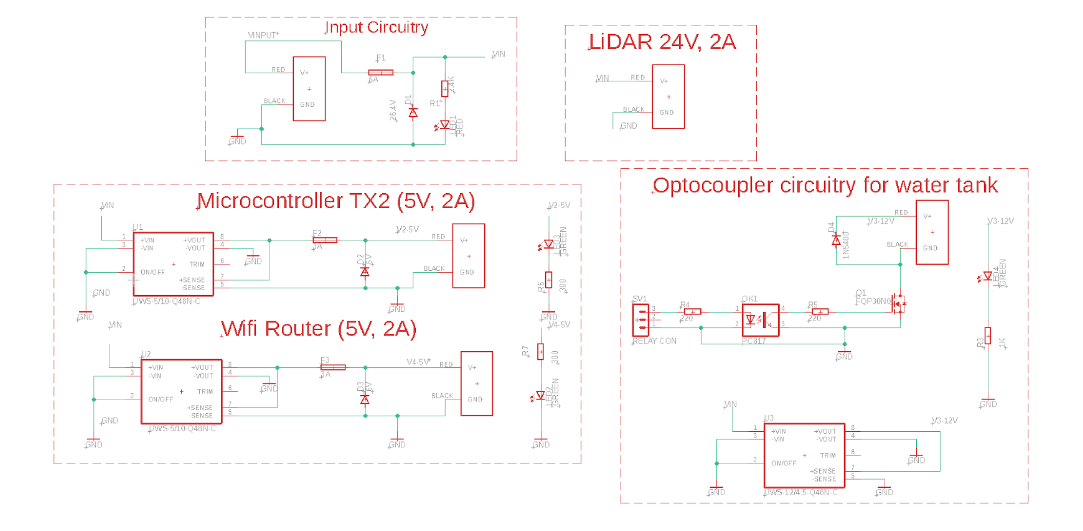