Spring Validation Demo (SVD)
Our SVD performs the full functionality of the Spring semester’s deliverables. The SVD took place in the Tepper AI MakerSpace. We utilized a Kinova Gen3 6 DOF arm, which was mounted to a table. We attached our custom end-effector to the arm as well as a RealSense depth camera. We set up a fake plant with easily visible and accessible green peppers. We also have a basket to collect the extracted peppers. An image of our SVD setup is shown below.
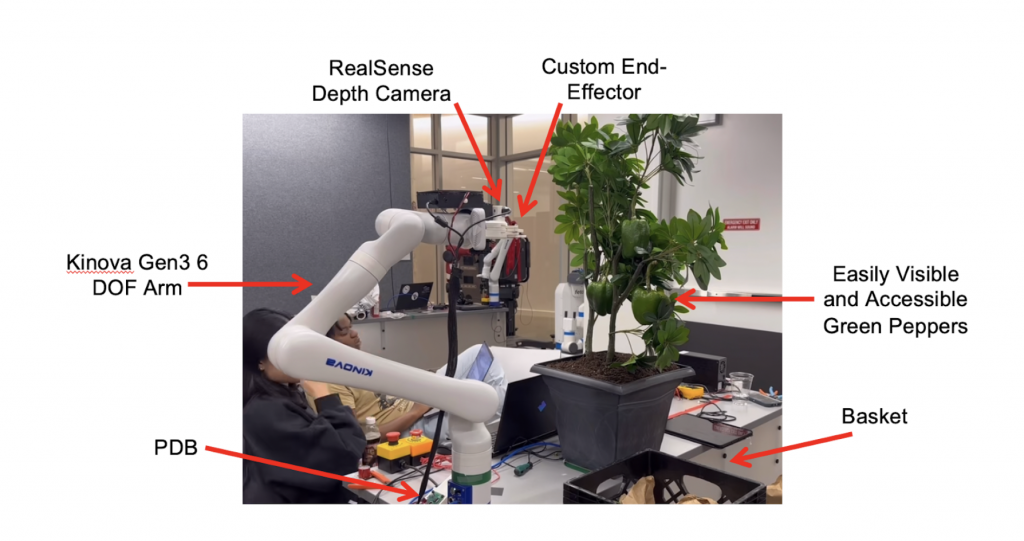
Procedure:
Setup:
- Attach six real green peppers to the fake plant setup. These peppers will be visible, easily accessible, and within the arm’s workspace.
- Place the plant within the workspace of the xArm6.
- Ensure all team members and audience are at least 10 feet away from the arm’s workspace.
Autonomous Operation:
- Once all team members and the audience are at a safe distance from the robot, one team member will initiate the system.
- Another team member will start a timer once the system begins its recognition procedure.
- Let the autonomous pepper harvesting process run.
- Once the green bell pepper has been placed in the basket, stop the timer. This will help to confirm that time requirements have been met.
- Processes 2-4 will be performed cyclically until all peppers have been harvested.
End Condition:
Once there are no recognizable peppers within the robot’s workspace, the demo will conclude.
Spring Test Plan Document:
Below is our Spring Test Plan document, which includes an overview of our Springtesting procedures.
Fall Validation Demo (FVD)
Our FVD will likely take place in NSH B-Level. The testbed will require setting up 4 fake plants. We will be using the Amiga base platform and the xArm6 robotic arm. We will mount the arm with our end-effector on the mobile platform in an upside-down configuration. The system will have a RealSense camera mounted on the end-effector.
Procedure:
Setup
- Have four fake pepper plants and at least one real green bell pepper on each plant. These peppers will be visible, easily accessible, and within the arm’s workspace.
- Tele-operate the Amiga base to have a plant in the xArm workspace.
- Ensure all team members and audience members are at least 10 feet away from the xArm’s workspace.
Autonomous Operation
- Once all team members and the audience are safe from the robot, one team member will initiate the system.
- Another team member will start a timer once the system begins its recognition procedure.
- Let the autonomous pepper harvesting process run.
- Lap the timer once a green bell pepper has been placed in the basket. This will help to confirm that time requirements have been met.
- Tele-operate the Amiga to move to the next location once the pepper(s) have been picked from the current plant.
- Repeat processes 2-5 to be performed cyclically until all peppers have been harvested.
End Condition
Once the Amiga reaches the end of the pepper plant row, the demo will conclude.
Verification Criteria:
- Robot successfully harvests each accessible pepper within 5 minutes.
- Avoid visible damage to 75% of the picked peppers (cuts/bruises).
- 0 injuries or cases of harm to the team members.
Quantitative Performance Metrics:
For our quantitative performance metrics, we hope to achieve all of our performance requirements. Although we already met some of our performance requirements in the Spring, we want to achieve them on our Fall testbed since we are stepping up the complexity of the environment to be more representative of the farm. We did change one of our performance requirements from the Spring Semester. Instead of handling stem constraints for PR.02.1, we will ensure that the generated trajectory avoids 100% of collisions with the ground and the amiga mobile base.
Graphical Representation:
The figure below shows a graphical depiction of the FVD setup. The testbed includes the Amiga mobile base, the xArm6, the end-effector, and fake plants with real peppers on it.
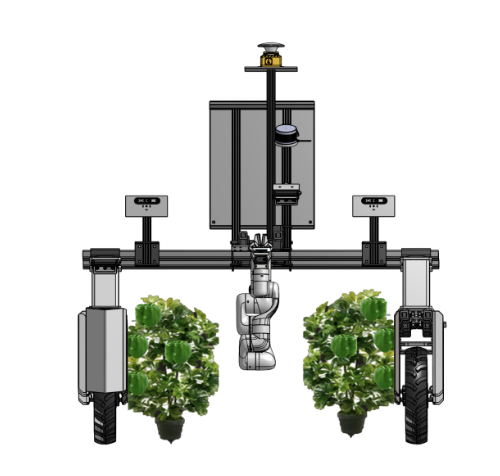
Fall Test Plan Document
Below is our Fall Test Plan document, which includes an overview of our Fall testing procedures.