System Requirements
Functional Requirement | Performance Requirement | Description |
[F1] Receive a list of testing locations from the user. | [M.P.1] Receive testing location within 5 minutes. | The robot follows a trajectory in the cornfield based on the GPS waypoints. |
[F2] Drive along a row of corn to testing locations. | [M.P.2.1] Maintain a lateral path error less than 15 cm over 10 m. [M.P.2.2] Reach testing locations within 2.5 m. | The robot visits each waypoint in the same row of corn. |
[F3] Identify cornstalk of suitable width. | [M.P.3]* Identify suitable cornstalk 50% of the time | The nitrate sensor should be inserted into the cornstalk such that the side perpendicular to the insertion angle should have a smaller axis (parallel to the longer side). |
[F4] Clean the surface of the nitrate sensor. | [M.P.4.1]* Clean 75% of the sensor surface. [M.P.4.2] Success rate is 75%. | After every insertion process, the nitrate sensor needs to be cleaned to make sure the residue from the insertion does not affect the nitrate readings for the next insertion. |
[F5] Calibrate the nitrate sensor. | [M.P.5]* Success rate is 80%. | Same as above. |
[F6] Grip the selected cornstalk of suitable width. | [M.P.6.1]* Success rate is 75%. [M.P.6.2] Grip within 10 cm of the ground. [M.P.6.3]* Success rate of gripping within 10 cm is 80%. | For inserting the nitrate sensor, the end-effector needs to grip the cornstalk within the given range. |
[F7] Insert the nitrate sensor into the cornstalk of suitable width. | [M.P.7]* Success rate is 50%. | |
[F8] Record readings from the nitrate sensor. | [M.P.8]* Filter out of range nitrate readings 90% of the time. | To check if the sensor is accurate, we are just checking if the readings are in range. Checking physical damage on the sensor is not in our scope. |
[F9] Remove the nitrate sensor from the cornstalk. | [M.P.9] Success rate is 90%. | |
[F10] Provide user with nitrate readings. | [M.P.10] Return nitrate readings within 5 minutes of completion. |
Functional Architecture
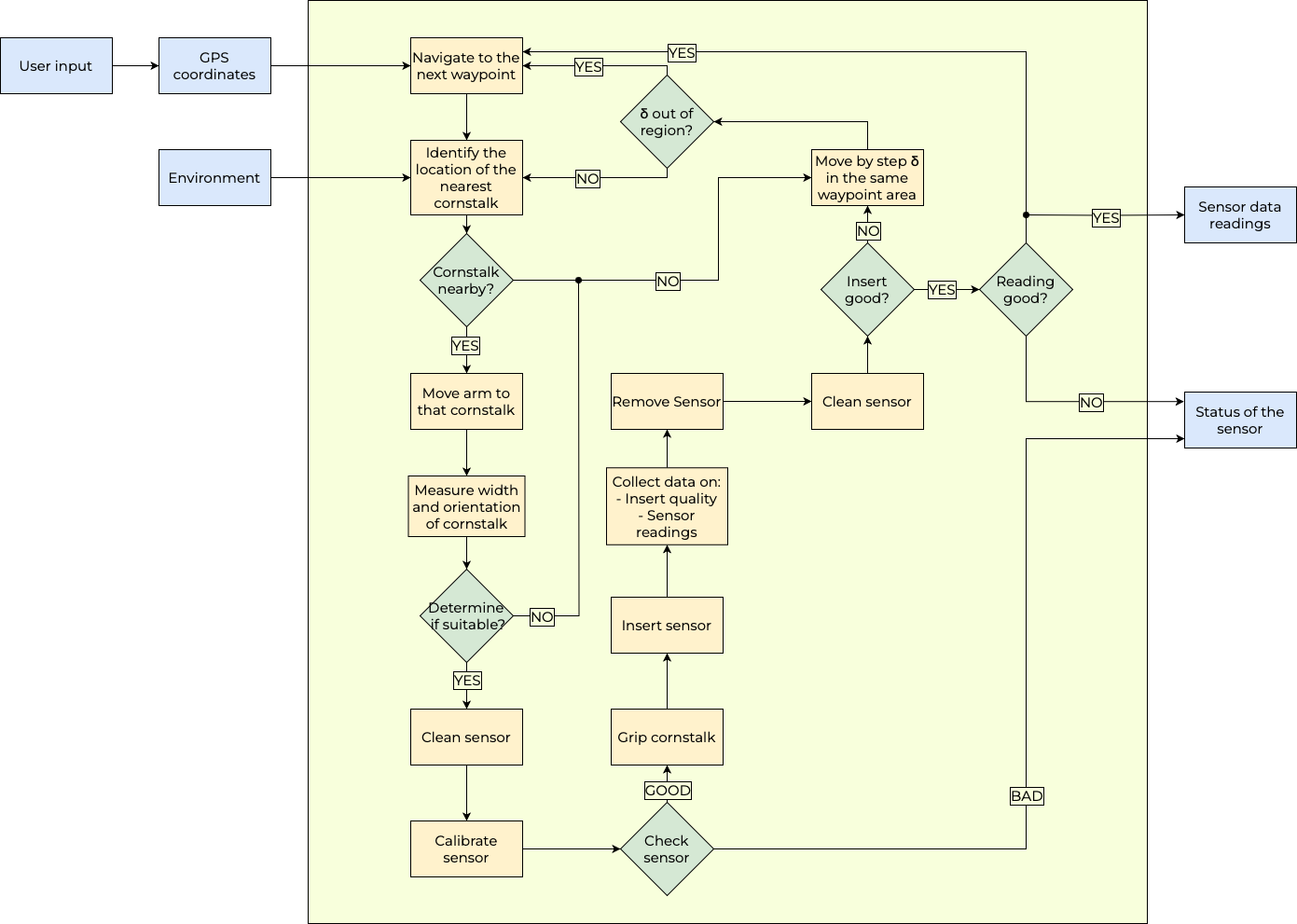
Cyberphysical Architecture
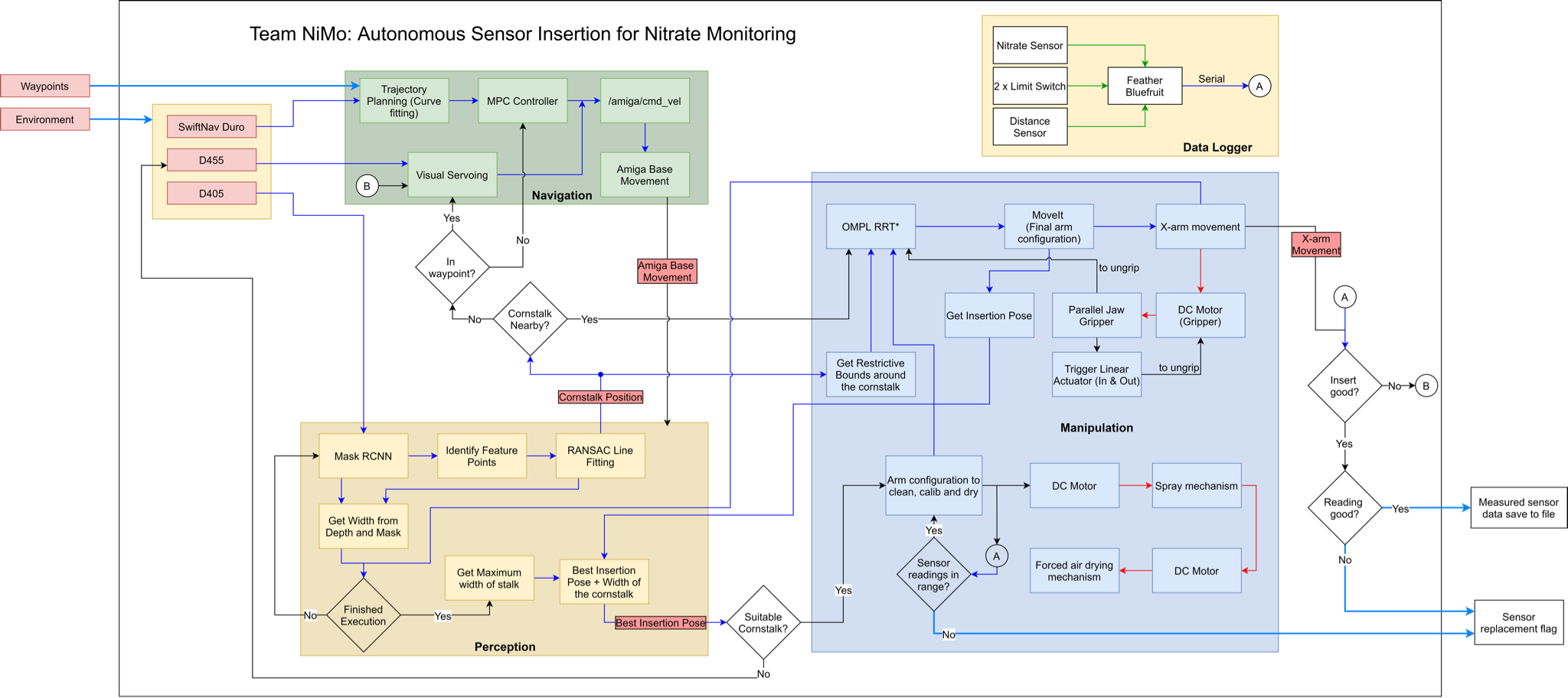
System Design Description
The system will be mounted on an Amiga mobile base with computer and power box. The UFactory xArm will be used for manipulation tasks, and the GPS, LiDAR, and Stereo camera will be used for navigation. The external mechanisms for cleaning and calibration will be mounted to the amiga mobile base. The end effector will be mounted to the xArm. Both the external mechanisms and end effector are described in more detail on the implementation page.
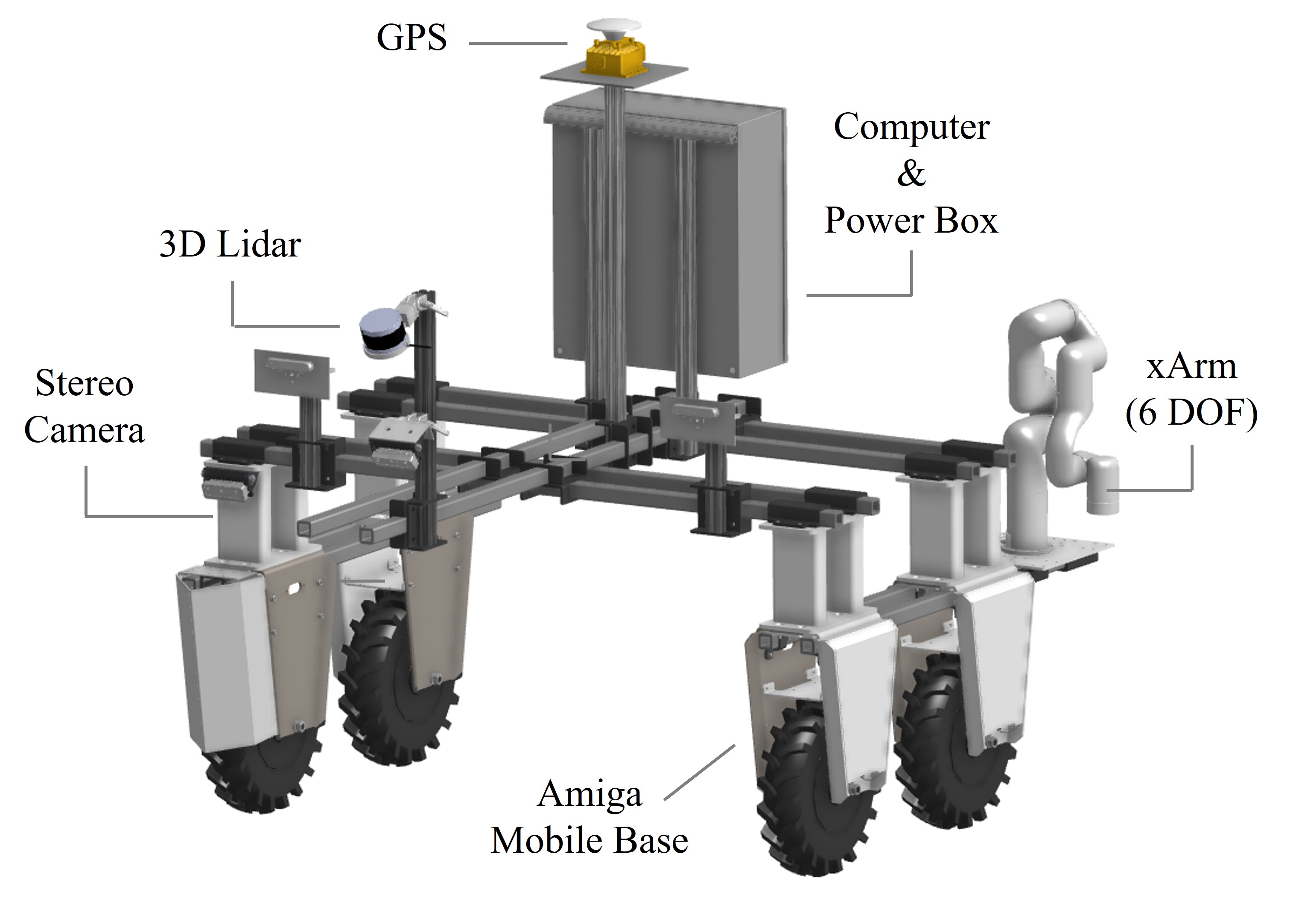