VTOL Subsystem
Our VTOL is a MakeFlyEasy Fighter VTOL that we purchased and assembled. The kit came with all the motors and flight control systems necessary for ensuring it would be capable of autonomous flight. We have made several minor modifications to allow us to fit both our perception and delivery subsystem onboard the vehicle.
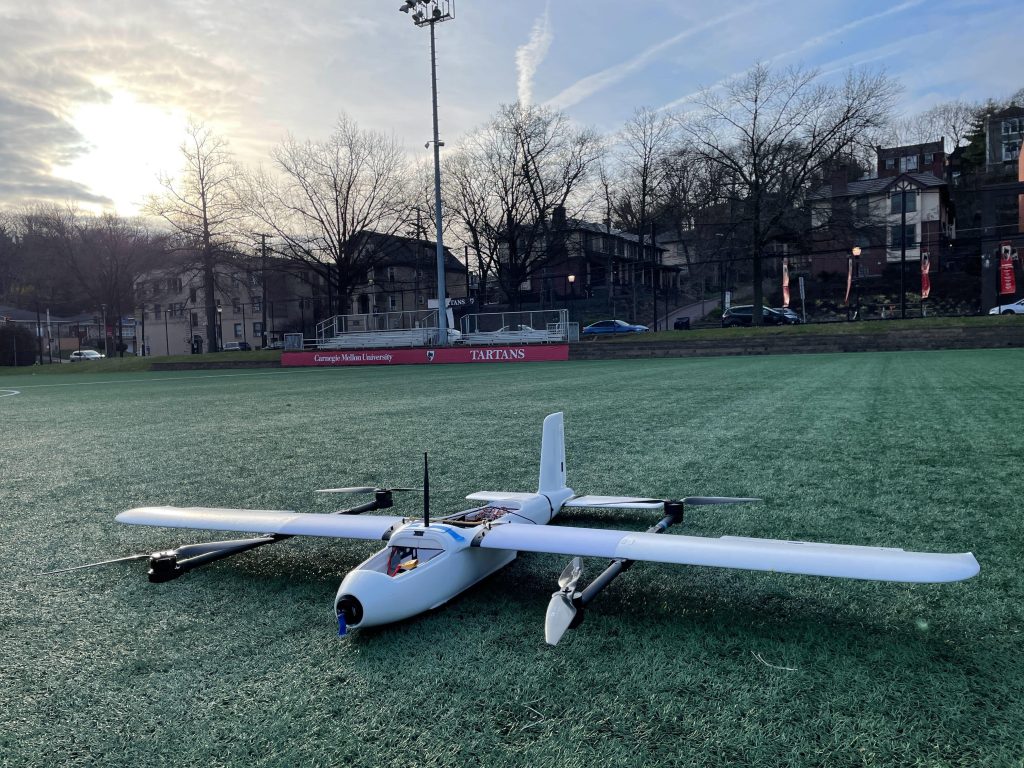
The platform was modified to fit a custom-built delivery mechanism. A hole was made in the base of the VTOL and the support structures inside were fit with detachable mounts for the mechanism. The platform was also used to collect data and hence a data logging module had to be fit inside. These two modifications needed to be used interchangeably to ensure development and sponsor requirement activities happen simultaneously. Below are images showing the two modified configurations of the VTOL.

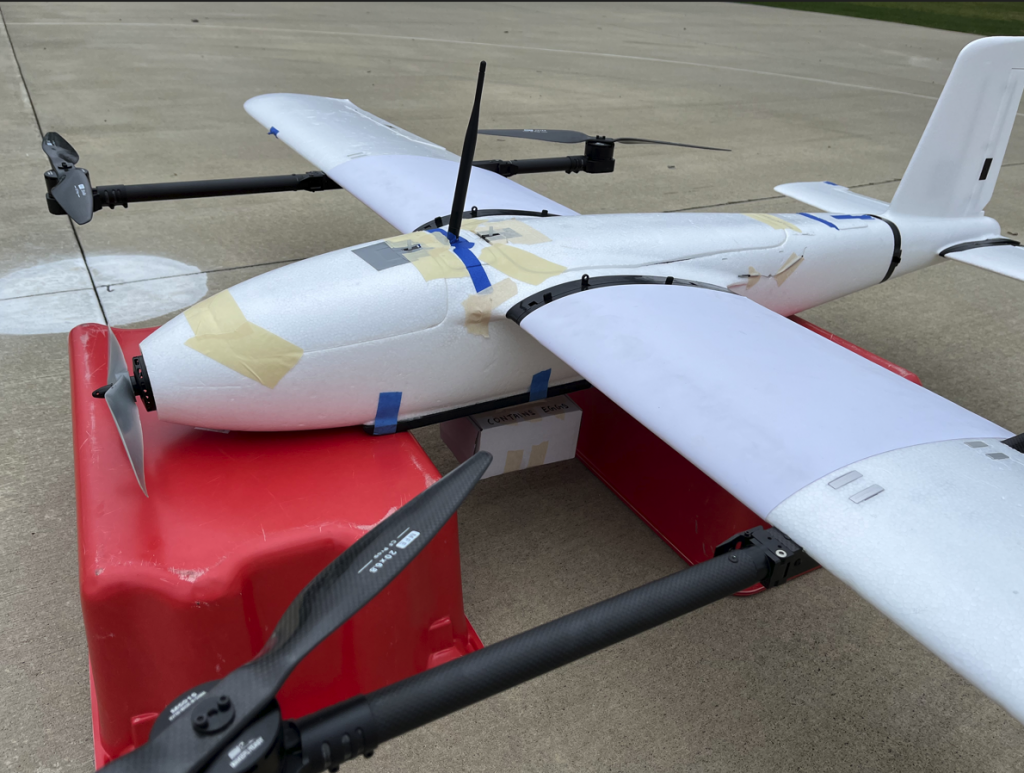
Perception Subsystem
OAK-D Camera
The camera we are using is an OAK-D camera from Luxonis. The camera has an onboard processor which provides us with the ability to perform vision processing on the camera itself instead of the companion computer.
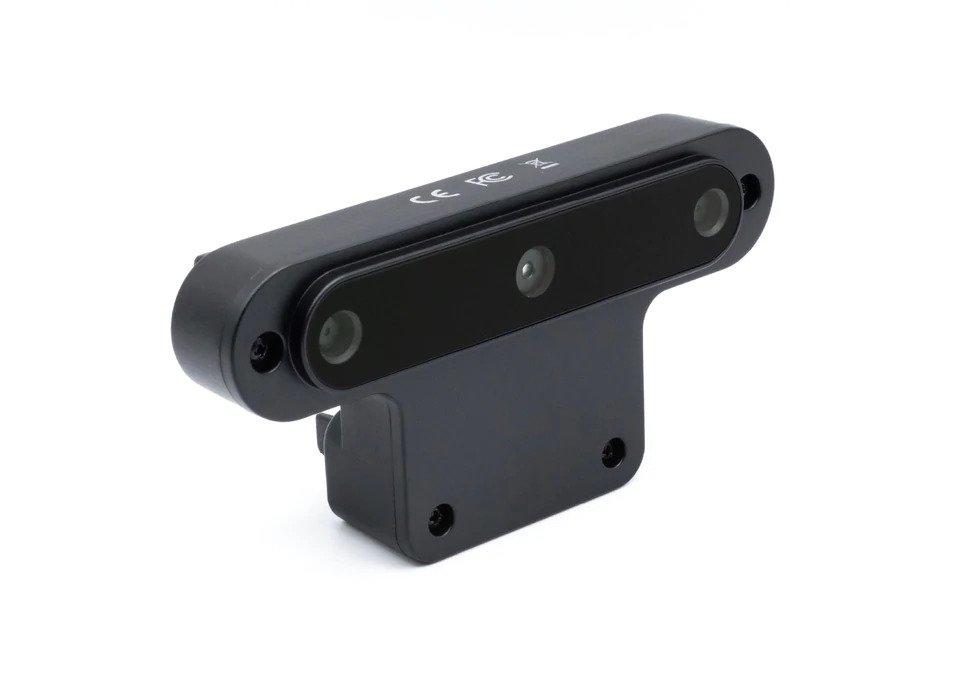
Camera Mount
In order to mount our OAKD to onto our VTOL we designed a mount that fits into the parachute cabin of our VTOL. The mount contains a locking mechanism allowing us to ensure that the camera will stay in place during flight.
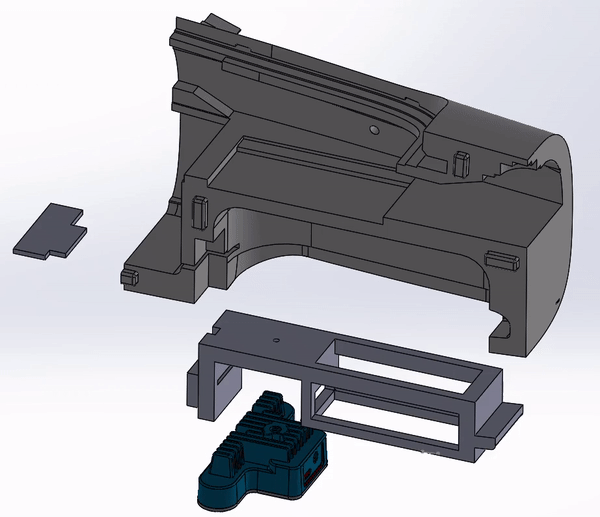
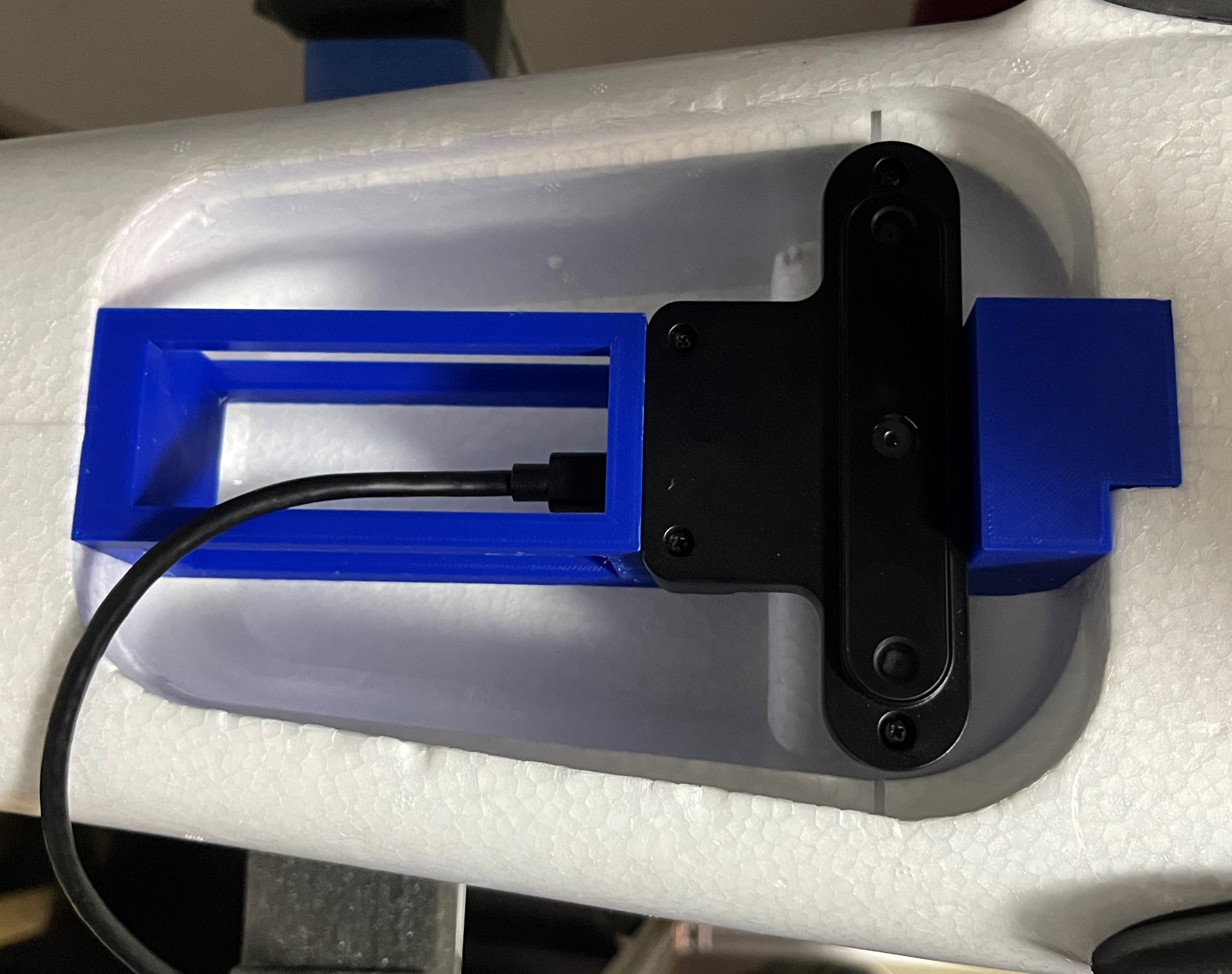
Delivery Subsystem
The Delivery subsystem went through a series of iterations over the course of the year. In the 1st semester of development (Spring 2021) the focus was on building a functional and morphological proof of concept to help us validate our design. With that done, the 2nd semester of development (Fall 2021) brought along rapid iteration, improvement, and integration of the design onto the body of the VTOL.
The section below will focus on Fall development progress. You can learn about the Spring development process at this page.
Delivery Subsystem Overview
MF.4 Deliver using a mechanism that holds, lowers, and releases the package at a target location without landing.
The delivery subsystem is broken into 3 main components that each address a key component of Mandatory Functional Requirement #4 (MF.4, above). When put together, they accomplish the goal of delivering a package at a target location without landing the VTOL. In the Fall semester, we developed a delivery subsystem that could accomplish MF.4 while integrating into the VTOL’s tight spatial and electromechanical constraints.
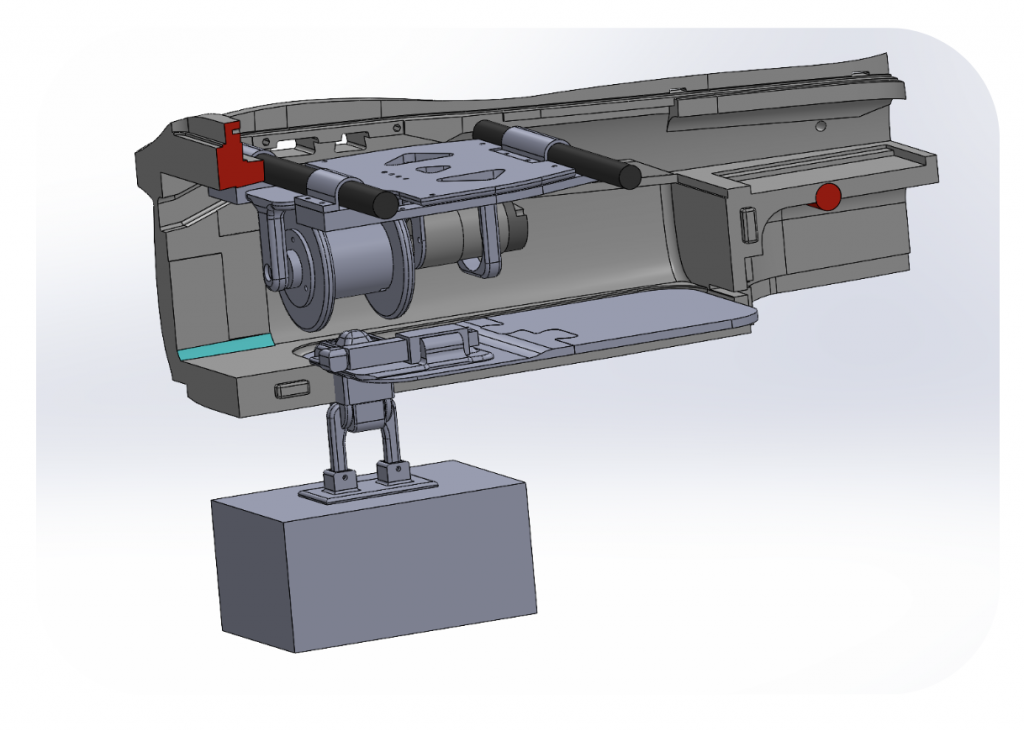
Lowering Mechanism | DC Motor-Powered Winch
The lowering mechanism is designed to lower the package at a steady rate when the VTOL is hovering in delivery position. A custom spool was built to interface with a DC motor (sourced here). The DC Motor was controlled by a an Arduino UNO using an Adafruit Motorshield. The cable used to lower the package was a paracord available here, that provided a lightweight solution with high tensile strength. The entire lowering mechanism was designed to be a standalone module – it could be inserted and removed from the fuselage at will so that we could access the wiring and other components as needed.
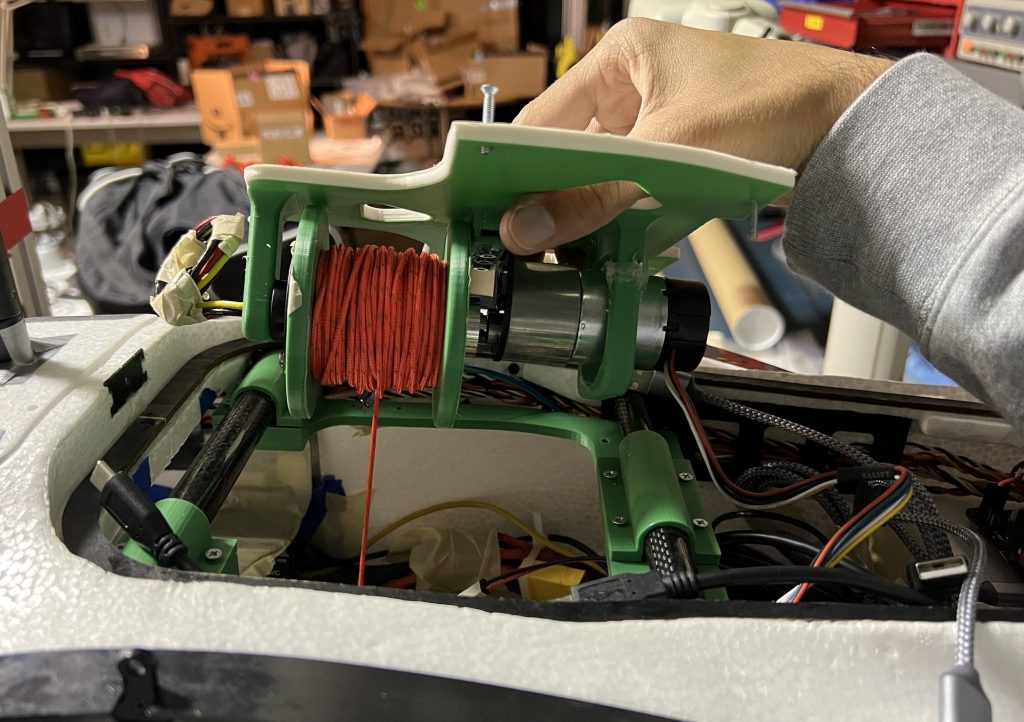
Holding Mechanism | Inserting a Holding Pin with a Linear Actuator
The Holding Mechanism is designed to passively hold the package during flight and prevent accidentally dropping the package during any phase of flight. It provides an extra layer of redundancy in ensuring the package is secure to the body of the VTOL.
We achieve this by inserting a pin into the release mechanism that holds the package snugly against the body of the VTOL. The linear actuator can remove this pin so that the package can be lowered for delivery. The linear actuator is powered and controlled through the same Arduino and motorshield combination identified above for the lowering mechanism.
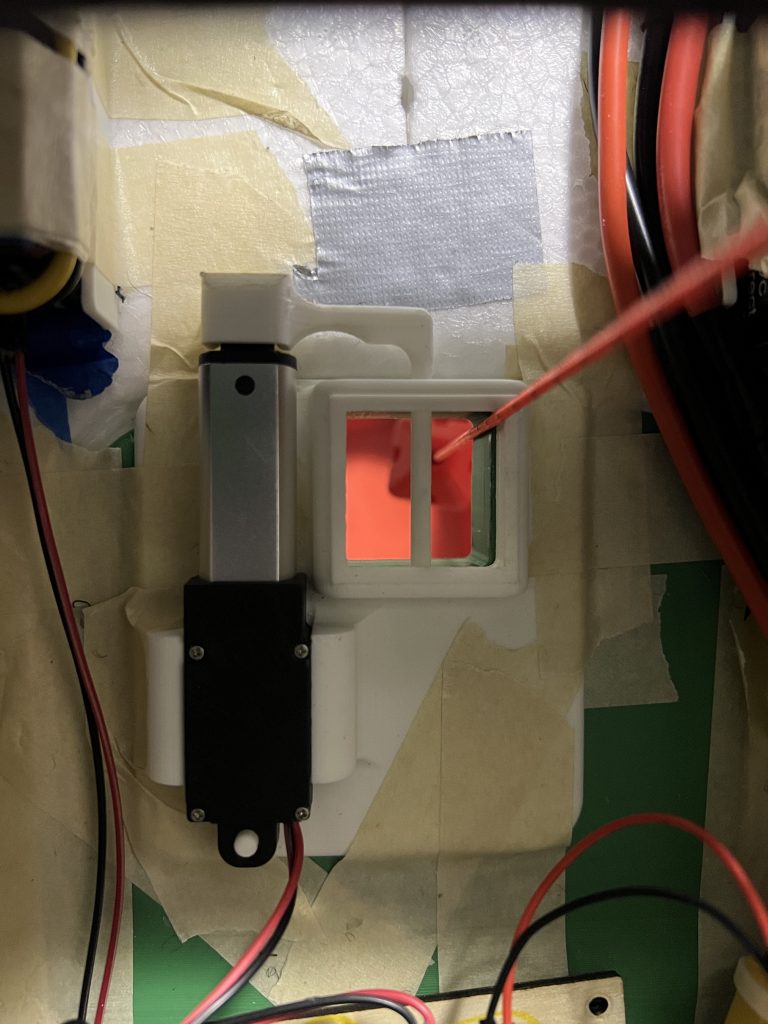
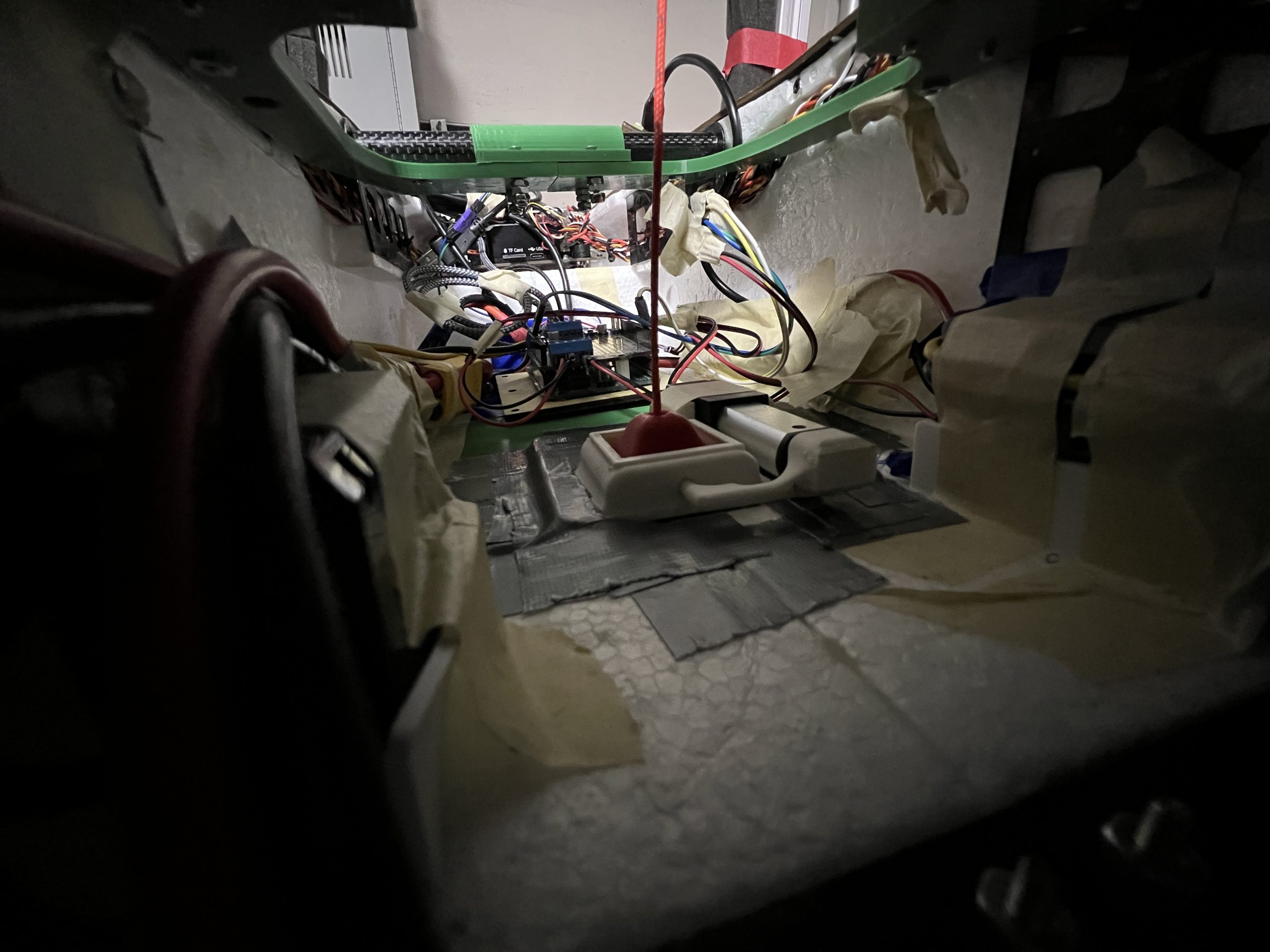
Release Mechanism | Passively delivery the package upon contact with the ground!
The release mechanism is designed to interface with the package to carry and release it during delivery. It relies on contact with the ground to separate from the package, and is specifically design to slide out along a desired axis. To ensure this, the ‘hook’ on the package is also a part of the design, as the release cable hook and package hook are designed to be coupled specifically with each other.
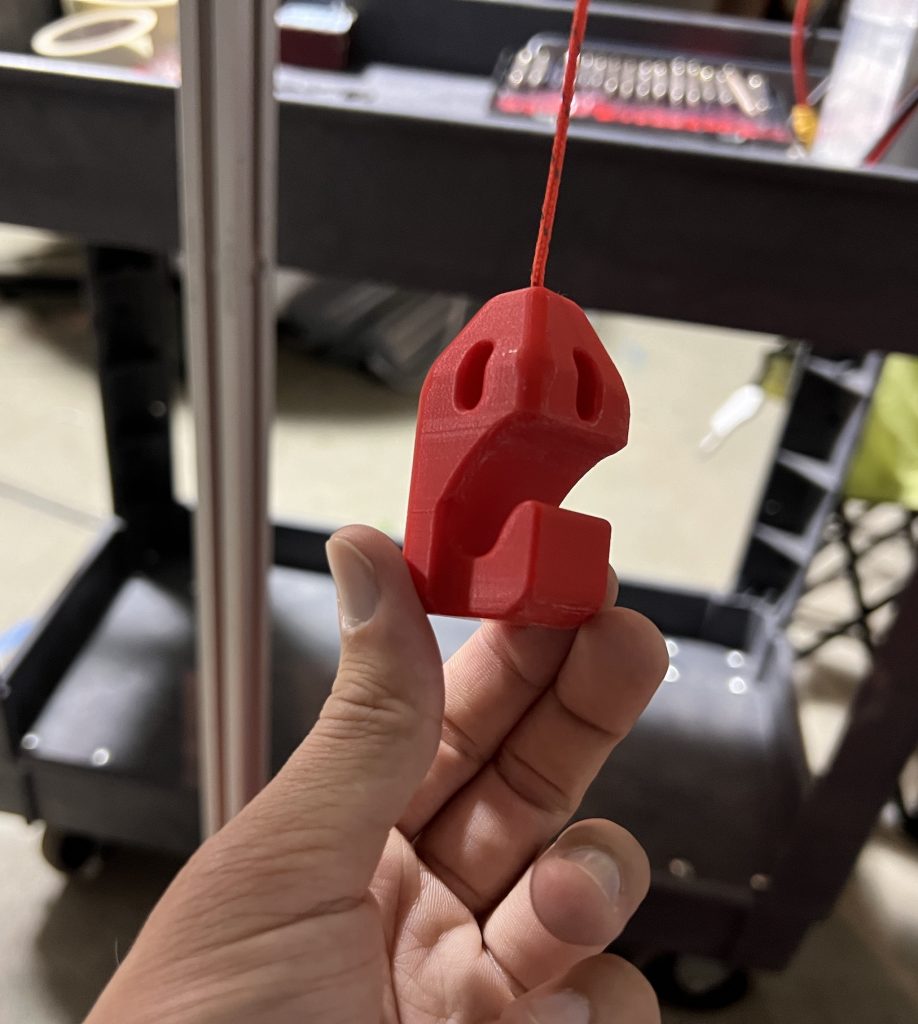
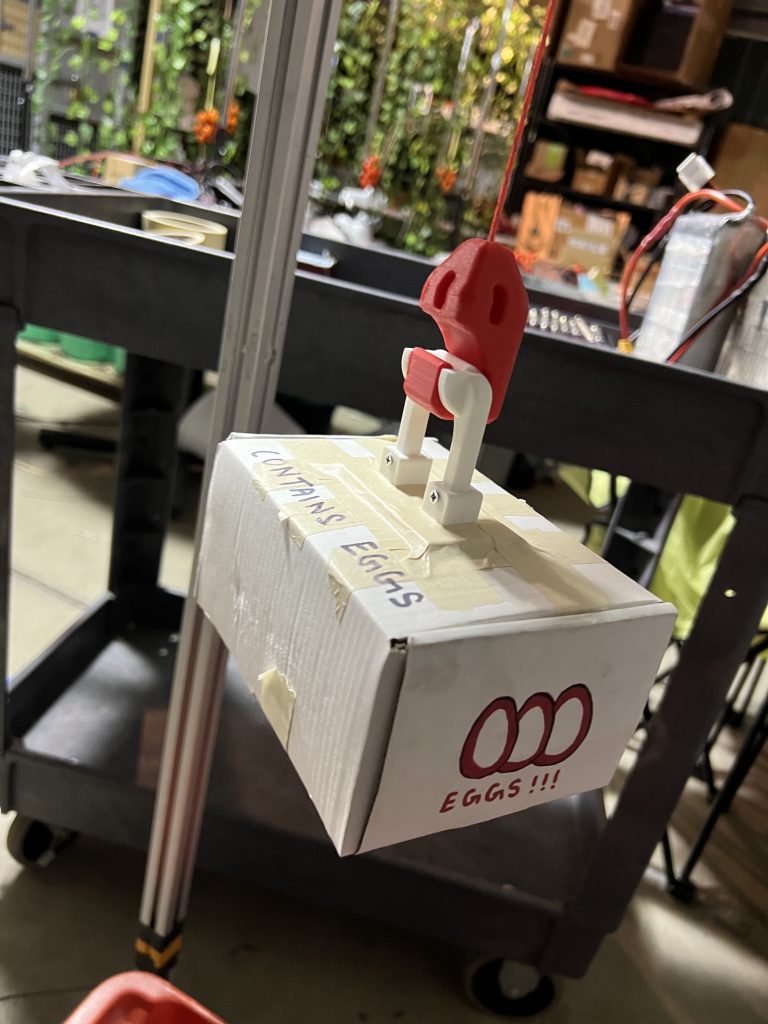
Data Logger
The requirement for the data logger was to record accurate GPS data, energy consumption, and wind speed and direction across multiple flights by varying set parameters. In order to have the same baseline as previous projects by our sponsors, the same set of sensors was used after designing the power supply circuit and appropriate connectors for integration on the VTOL.
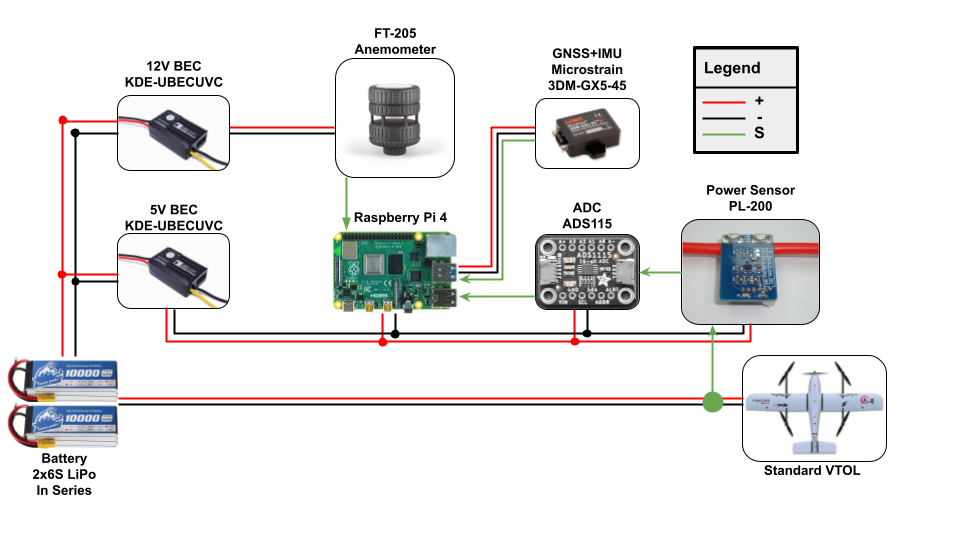