In modern hospitals, logistics operations play a crucial role in maintaining the efficiency and
sterility of operating rooms (ORs). Surgical professionals rely on the timely delivery of medical
items to ensure smooth operations, while logistics specialists are responsible for restocking
supplies in supply rooms and corridors. These tasks are essential but resource-intensive,
particularly given the limited workforce available in many hospitals. Addressing this challenge,
UPMC proposed the idea of leveraging robots to automate hospital logistics, leading to the
development of the Operating Room Bot (ORB) system.
The ORB system is designed to address two specific use cases: delivering medical items
directly to ORs during surgeries and restocking supplies on OR shelves. These use cases cater to
the distinct needs of surgical professionals and logistics specialists, aiming to improve overall
operational efficiency. The system is developed as a robotic mobile manipulator using the Fetch
robot, equipped with a hardware-agnostic ROS2-based software stack. This stack is designed to
be adaptable and scalable, enabling the ORB system to integrate seamlessly into dynamic
hospital environments while operating alongside human staff safely and efficiently.
Key features of the ORB system include autonomous navigation in cluttered environments,
safe interaction with human workers, and the ability to handle task-specific workflows for
delivery and restocking. By introducing robotic automation into hospital logistics, the ORB
system not only reduces the workload of hospital staff but also ensures a consistent and reliable
support system for critical medical operations.
Retrieval Use Case
In hospital operating rooms, maintaining sterility and efficiency is crucial for successful
surgical procedures. However, logistical challenges such as delivering essential medical supplies
during surgeries and restocking items in supply rooms place a significant burden on hospital
staff. The Operating Room Bot (ORB) system is designed to address these challenges by
introducing a robotic solution capable of autonomously navigating hospital environments and
performing logistics tasks alongside human workers.
One of the primary use cases of ORB is the delivery of medical supplies to operating rooms.
For instance, during an ongoing surgery, a surgeon might require additional sterile water. In a
traditional setup, a nurse or assistant must leave the operating room, locate the item in a supply
room, and bring it back. This process not only interrupts their workflow but also risks
compromising the sterility of the operating room. With ORB, this task becomes seamless. Upon
receiving the request, ORB autonomously navigates through the hospital to the supply shelf
containing sterile water, identifies the correct item, retrieves it, and delivers it promptly to the
operating room. This ensures timely delivery while maintaining the sterility of the operating
environment and allowing the surgical team to focus entirely on the procedure.
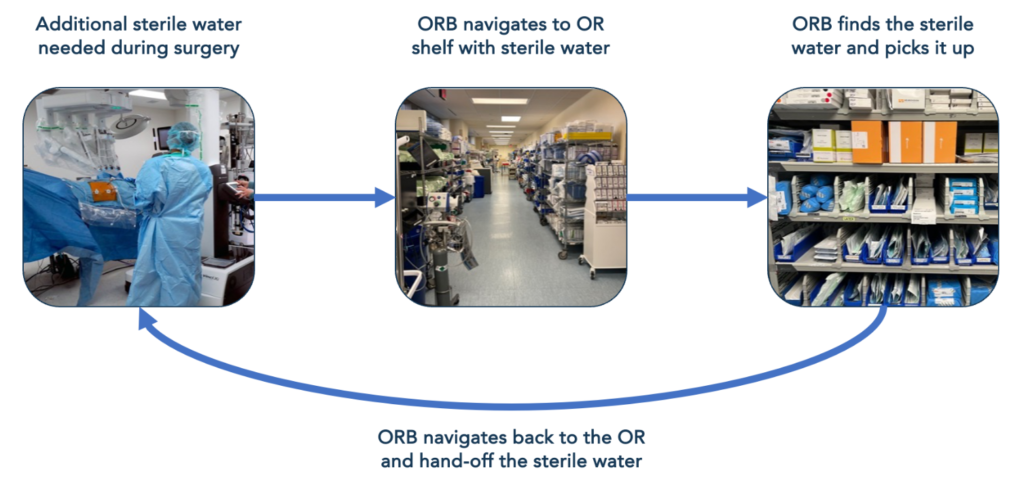
Restocking Use Case
Restocking supply shelves is another area where ORB improves efficiency. Traditionally,
hospital staff are required to retrieve supplies from central storage and manually organize them
in OR corridors or supply rooms. ORB automates this task by autonomously fetching items from
storage and placing them in their designated locations. This not only ensures supplies are readily
available but also reduces the workload of logistics staff, enabling them to focus on more
complex responsibilities. The system’s ability to operate safely in cluttered environments and
interact seamlessly with human workers is a key feature that enhances its utility in busy hospital
settings.
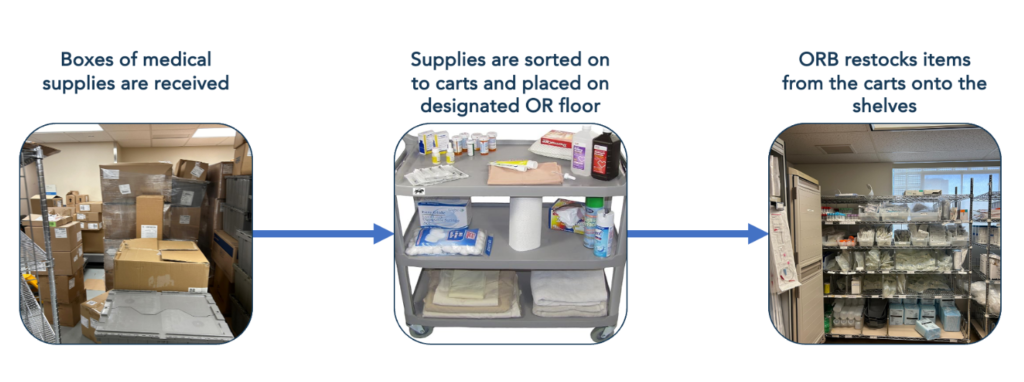