Fall 2021 (Up-to-date, Oct 4th)
Our test plan until FVD can be found here and 1-pager for FVD here
1-pager for SVD can be found here
Spring 2021 (Updated)
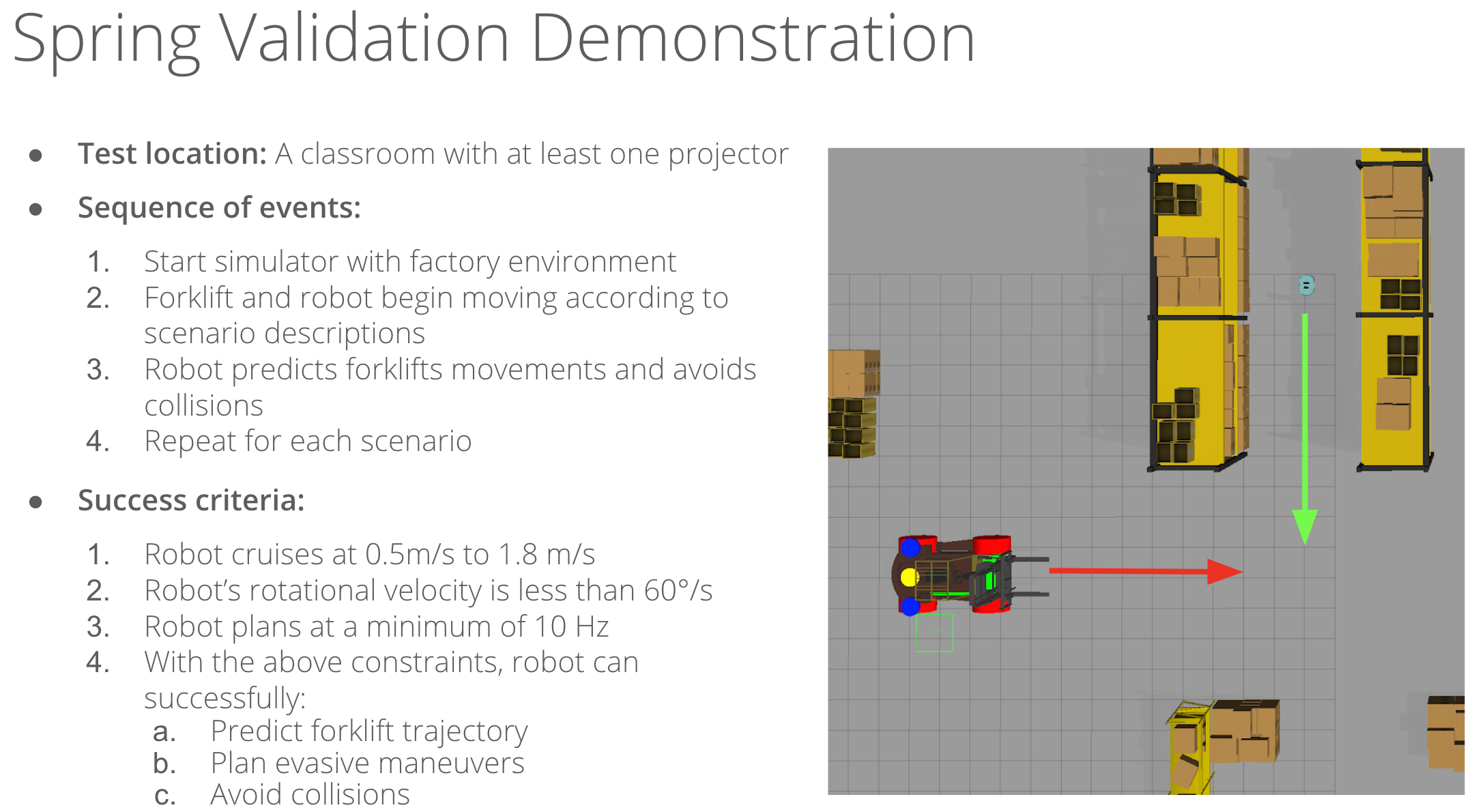
Fall 2021 (Updated)


Spring 2021
Virtual System Validation:
A. Demo Conditions:
- Location: In simulation
- Equipment: A computer system or cloud server with Gazebo, ROS and COLA predictive avoidance packages installed
- Operating area: Simulated 92*64 m factory environment (virtual)
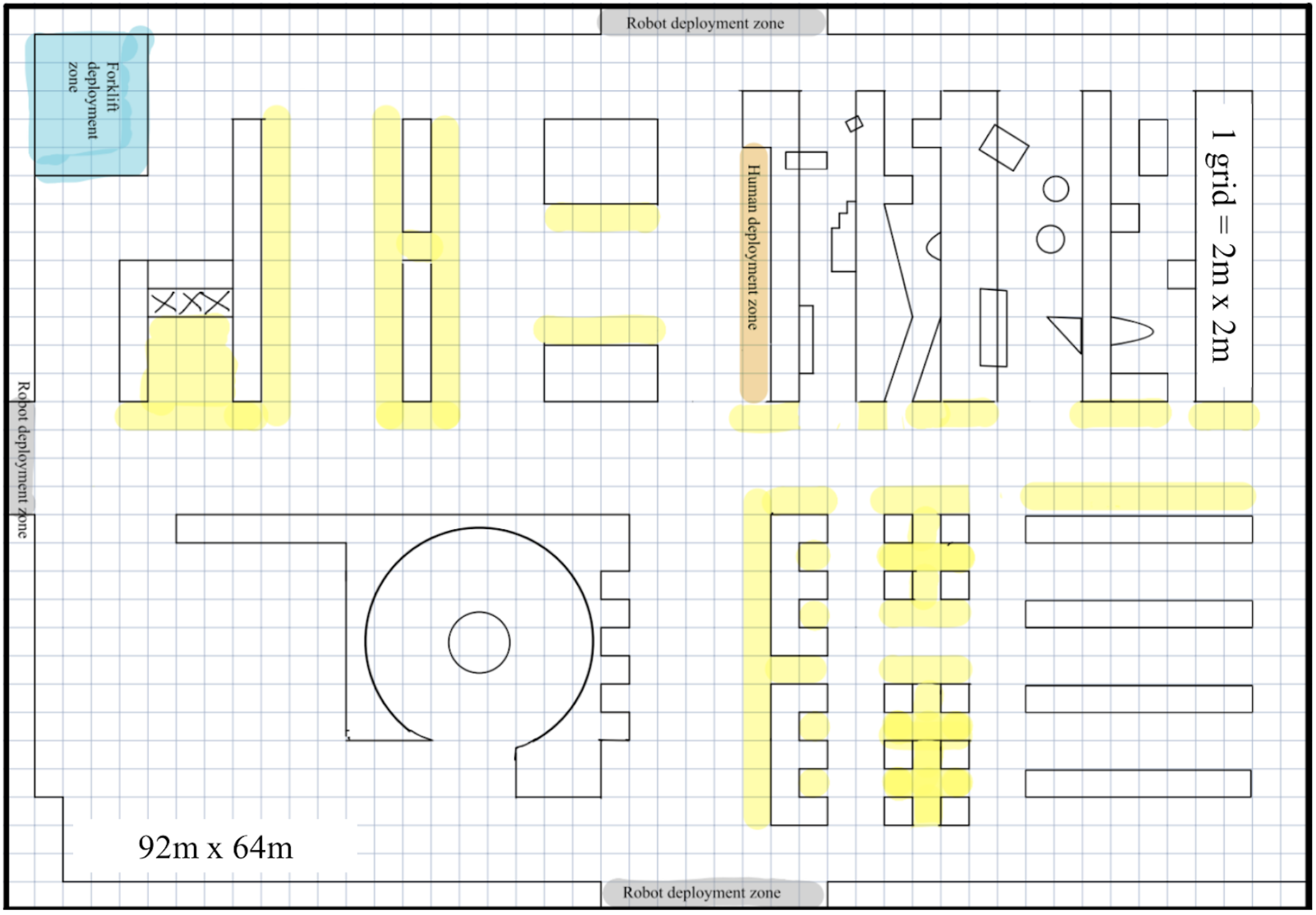
Figure 1: Floor plan for the virtual factory environment
B. Procedure:
- The user starts ROS core and simulation
- Simulator loads the floor plan for the factory, and launches the visualization tool.
- Simulator launches pedestrians and forklifts, following their fixed paths and routines
- Simulator launches one robot, and publish waypoints and the static map to robot
- Robots plan global paths and start moving
- Robots continuously receive localization and noisy obstacle observation from simulator
- Robots avoid obstacles according to its predicted trajectories of obstacles
- System stops after a certain duration of time
C. Objective & Requirements to Demo:
- To demonstrate the simulation system and simulated environment with obstacles
- To demonstrate the robot’s ability to plan paths and follow them
- To demonstrate the predictive avoidance algorithm (showing robots dodging obstacles using predicted trajectories)
- To validate M.P.1-3: Robot speed will be above 0.5m/s and below 1.8m/s if no obstacle is detected
- To validate M.P.5: Robots should receive localization and observation in at least 10 Hz, and send back control signals to the simulator in at least 10 Hz
Fall 2021
Real-Life System Validation:
A. Demo Conditions:
- Location: Any location with flat ground, sufficient lighting and high enough ceiling (over 2.5 m).
- Equipment: TurtleBot, obstacle action figures/toys, overhead camera, lights
- Operating area: 2*2 m flat ground
B. Procedure:
- Setup overhead camera and place markers on top of robot/obstacles for ground truth gathering
- Place robot and one or more obstacles in testing ground
- Manually drive robot and/or obstacles
- Obtain robot estimation of obstacle positions and classifications for demo duration
- Obtain ground truth position data of robot and all obstacles from overhead camera readings for demo duration
- Use measurement and ground truth data for visualization/plotting
- Evaluate detection (position) and classification accuracy
C. Objective & Requirements to Demo:
- To Validate M.P.6: Classify obstacles of interest with mAP of at least 60%
- To Validate M.P.7: Detect positions of obstacles of interest within 0.1 m accuracy
- To Validate M.P.8: Detect obstacles of interest within a range of 3 m
- To Validate: M.P.9 Output results of positioning and classification within 100 ms per frame
Virtual System Validation:
A. Demo Conditions:
- Location: In simulation
- Equipment: A computer system or cloud server with Gazebo, ROS and COLA predictive avoidance packages installed
- Operating area: Simulated 92*64 m factory environment (virtual)
B. Procedure:
- The user starts ROS core and simulation
- Simulator loads the floor plan for the factory, and launches the visualization tool.
- Simulator launches pedestrians and forklifts, following their fixed paths and routines
- Simulator launches robot fleet, and publish waypoints and the static map to robots
- Robots plan global paths and start moving
- Robots continuously receive localization and noisy obstacle observation from simulator
- Robots avoid obstacles using all three avoidance algorithms
- System stops after a certain duration of time and calculates resulting productivity
- System repeats the previous steps in naive avoidance mode without any classification and prediction, and computes nominal productivity
C. Objective & Requirements to Demo:
- To demonstrate all three avoidance algorithms (predictive, conservative, reciprocal)
- To validate M.P.4: Robot fleet should have productivity increased by >5% when using classification-based predictive/reciprocal avoidance compared to nominal productivity using only naive avoidance
- To validate M.P.5: Robots should receive localization and observation in at least 10 Hz, and send back control signals to the simulator in at least 10 Hz