The customized tool design and integration involve the following steps:
- Design of the Gripper and Cutter
- Motor Integration and Setup with the Robot Stack
- Testing of Integration between Robot and Tool
February Progress Update
Figures 1, 2, and 3 show initial prototypes of the tool.


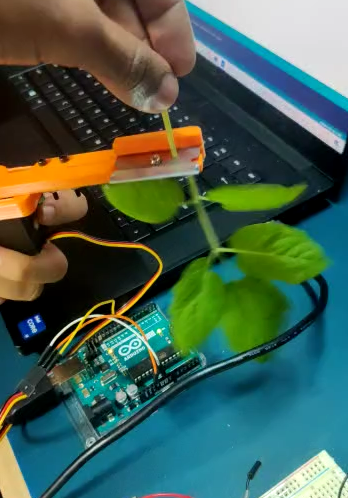
March Progress Update
Further iterations to the tool design were made. Figures 4, 5 show the pollinator and harvester iterations.
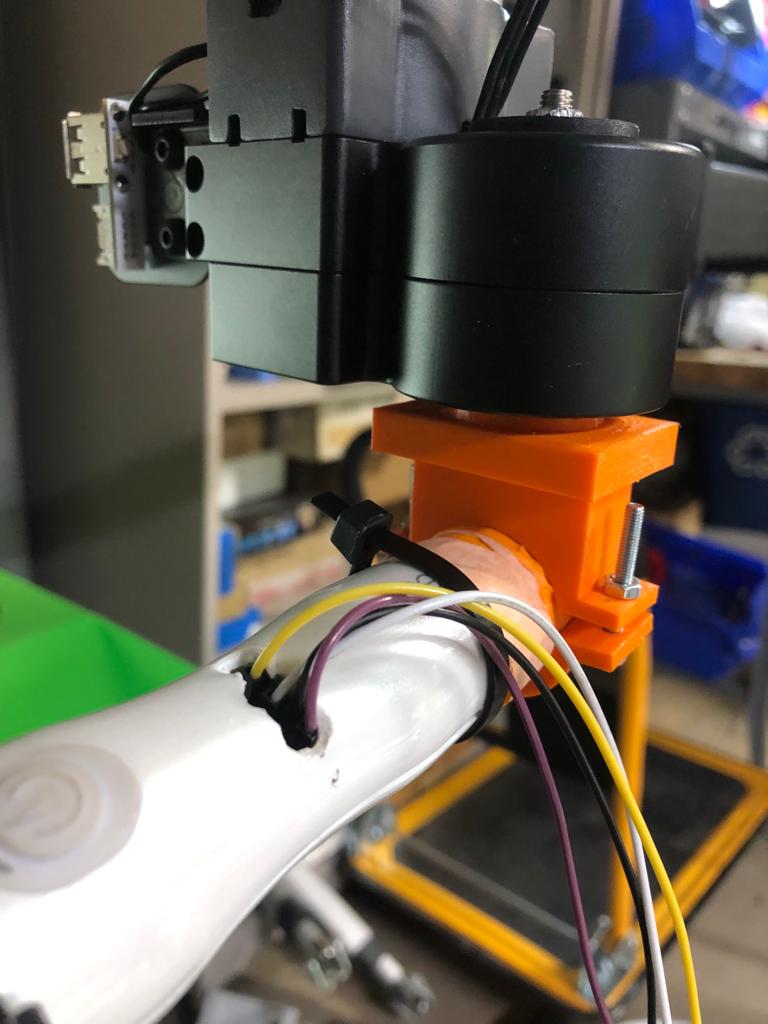
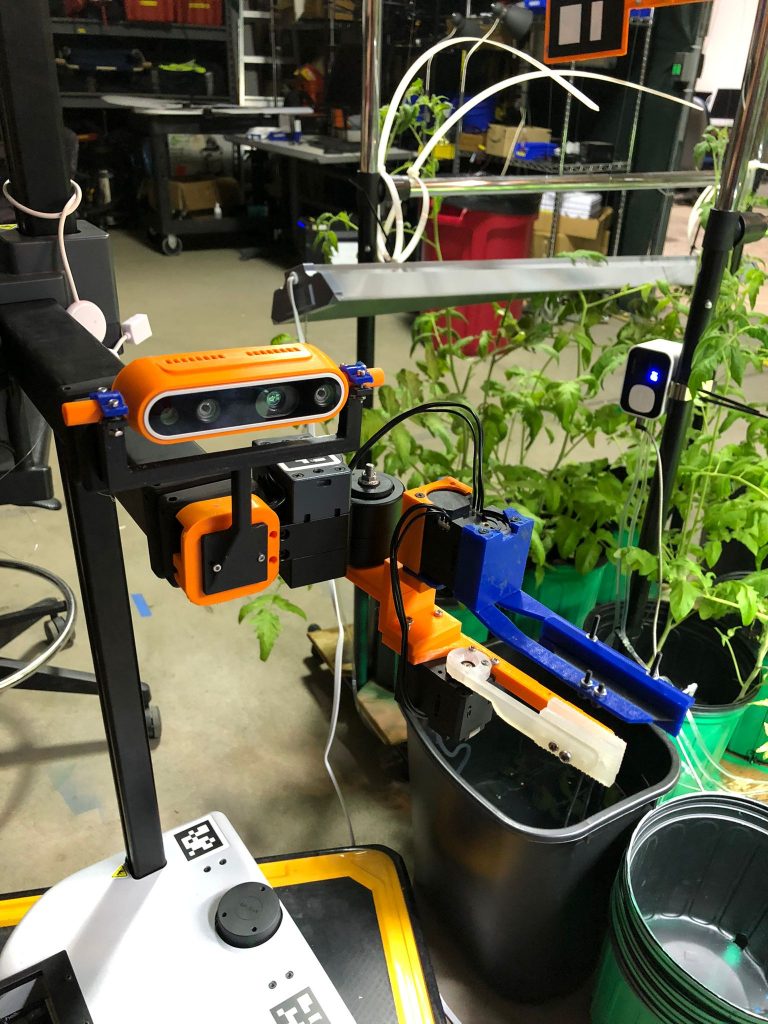
April progress update
We have currently finished the iteration and design phase of the tool. Both the tools have a common connecter to the robot such that change of tool can be easy and not time consuming. The tool files were then integrated to the robot urdf for integration with manipulation and the behavior planner (Figures 7, 8).
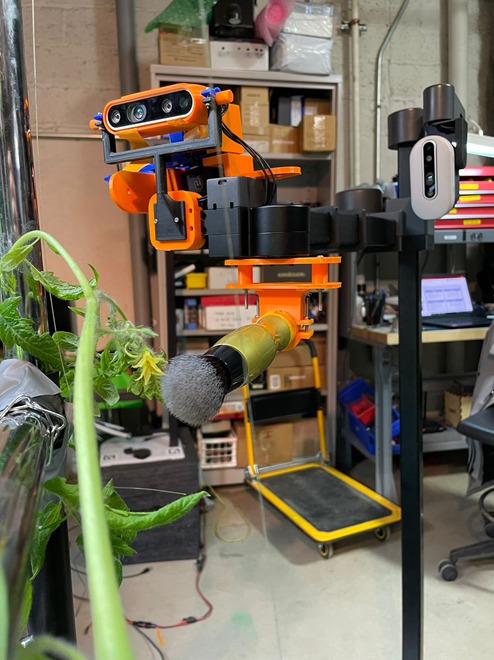
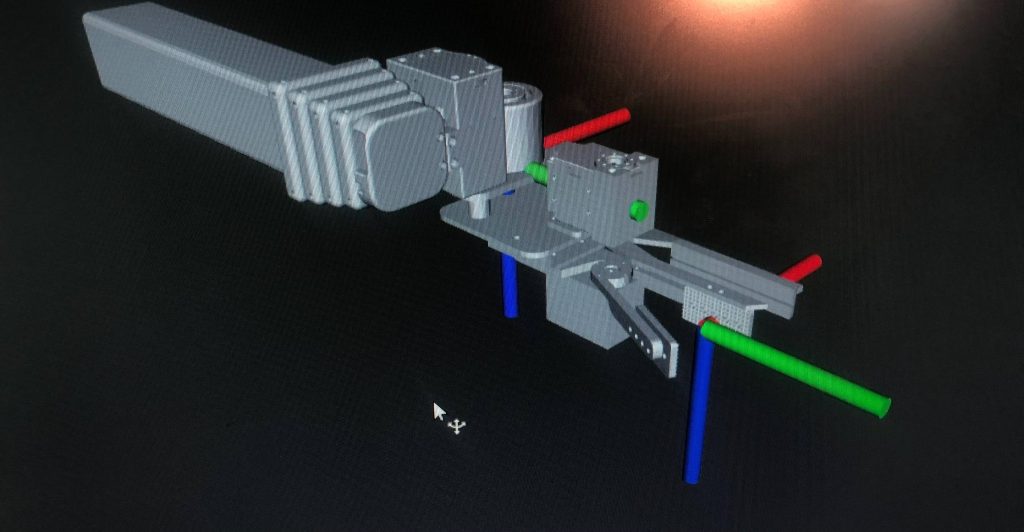
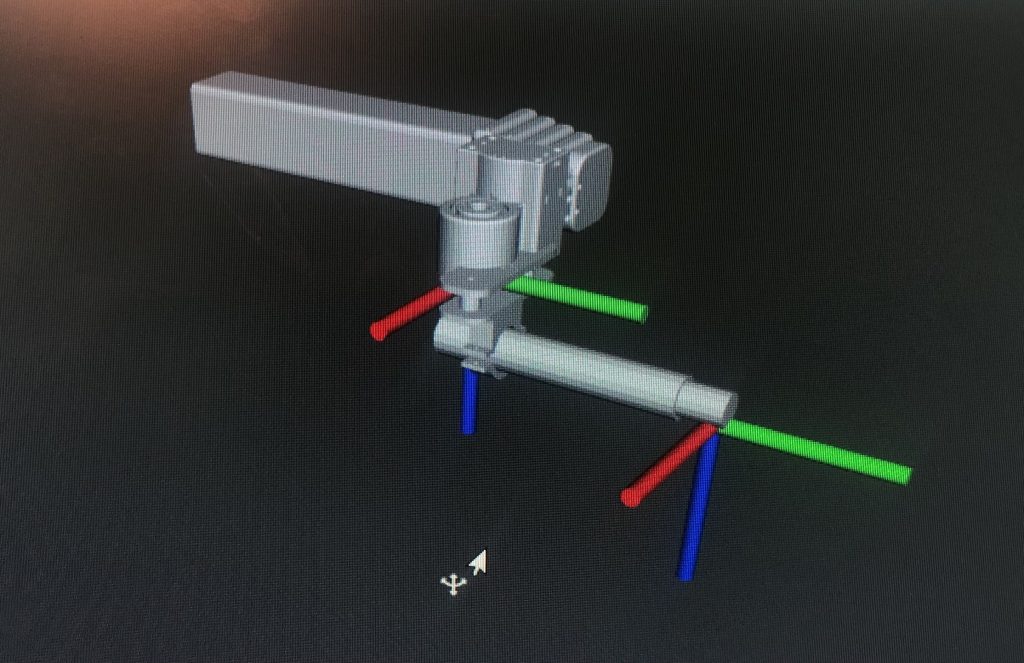
May progress update
The tool has been integrated with manipulation subsystem and the behavior planner. This allows for easy control of the tool. Tests show that gripper can carry weight up to 500 gm. The cutter was tested on tomatoes with stem thickness up to 1 cm diameter. The system does fail in some cases – where motor commands are dropped by the stretch driver leading to reduced motor torque or synchronous movements of robot. (fails around 2/10 times)
For pollination, when localized accurately, pollination has 100% success rate. Successful pollination refers to visible shaking / movement of the stems or flowers due to the tool.
Fall update – Final tool!
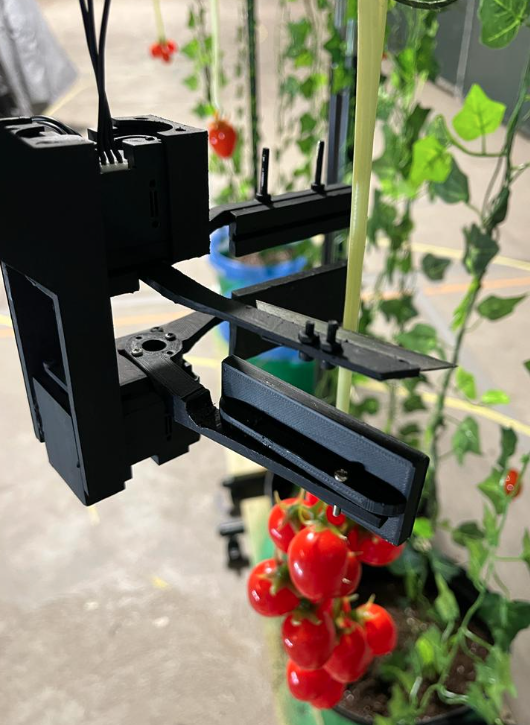