The SVD demonstration will need all 5 members of the team to be present and will take place outside the cage. The Hello Robot, operator’s computer, customized tools, and the test setup will be needed for the demonstration.
Procedure :
- To show pollination, navigation and perception
- Robot is placed at the start of the test environment’s first row.
- Reactive navigation package is launched. It follows the path as shown in Fig 1.
- Perception package is launched.
- Bounding boxes for flowers for the first row are obtained as shown in Fig 2.
- Robot stops at the bounding box location as shown in Fig 2.
- Robot arm reaches the bounding box location as shown in Fig 2.
- Robot arm reaches the POI location(given via aruco markers) as shown in Fig 3.
- Robot performs the pollination test (as mentioned in test 11) as shown in Fig 4.
- Robot navigates to the next pollination point and repeats this for two more instances.
- Robot reaches the end of the row, does row switching using aruco markers.
- Robot navigates through one more row and then stops.
- To show harvesting, navigation and perception
- Robot is placed at the start of the test environment’s first row.
- Reactive navigation package is launched. It follows the path as shown in Fig 1.
- Perception package is launched.
- Bounding boxes for fruits for the first row are obtained as shown in Fig 2.
- Robot stops at the bounding box location as shown in Fig 2.
- Robot arm reaches the bounding box location as shown in Fig 2.
- Robot arm reaches the POI location(given via aruco markers) as shown in Fig 3.
- Robot performs the harvesting test (as mentioned in test 10) as shown in Fig 5.
- Robot navigates to the next harvesting point and repeats this for two more instances.
- Robot reaches the end of the row, does row switching using aruco markers.
- Robot navigates through one more row and then stops.
- To show harvester tool capability
- Tomato bunch is placed near the robot end effector such that the stem is in between the gripper pads as shown in Fig 5.
- Run harvesting program which will activate the gripper and cutter sequence as shown in Fig 5.
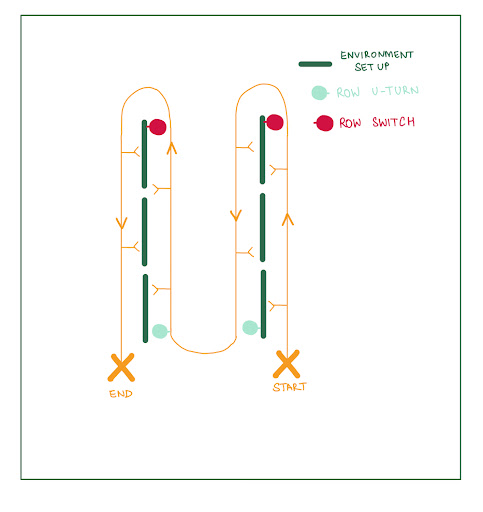
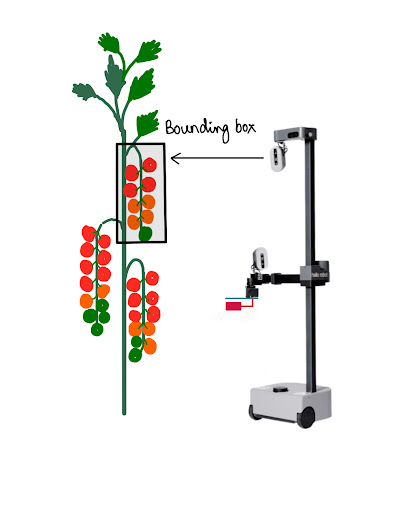
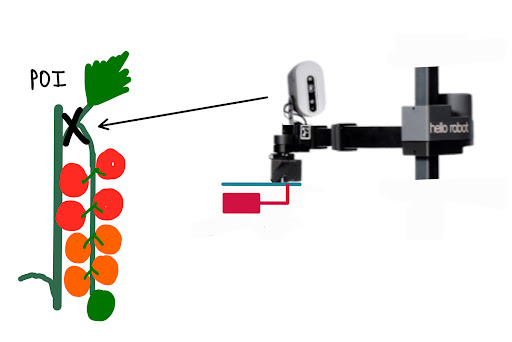
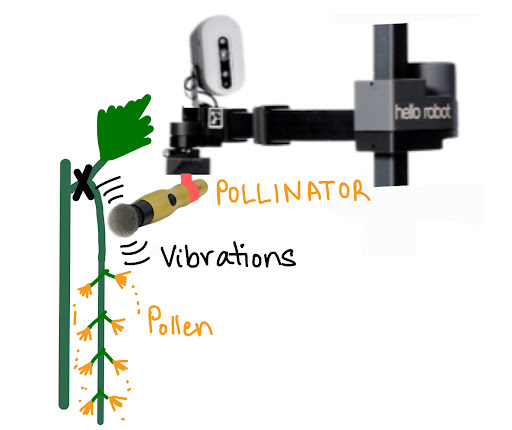
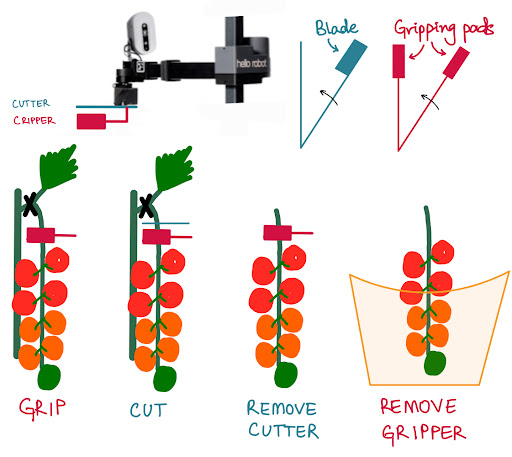
Validation
- The robot must track the rows within ±15 cm accuracy (M.P.1) while not colliding with plants and pots (M.P.2).
- The robot must successfully change rows when at the end of one row (D.P.1).
- The robot detects tomatoes/flower clusters with a success rate of 60%. (M.P.3, M.P.5).
- Clusters of flowers / tomatoes located to within 10cm (Euclidean) (D.P.3, D.P.4).
- The harvesting tool should cut the stem in two or less passes (D.P.6).
- The payload capacity of the harvesting tool should be atleast 500g (M.N.1, M.N.2).
- Flowers will be preserved 60% of the time (D.P.4).
Fig. 5 shows the performance evaluation following SVD and SVD Encore.
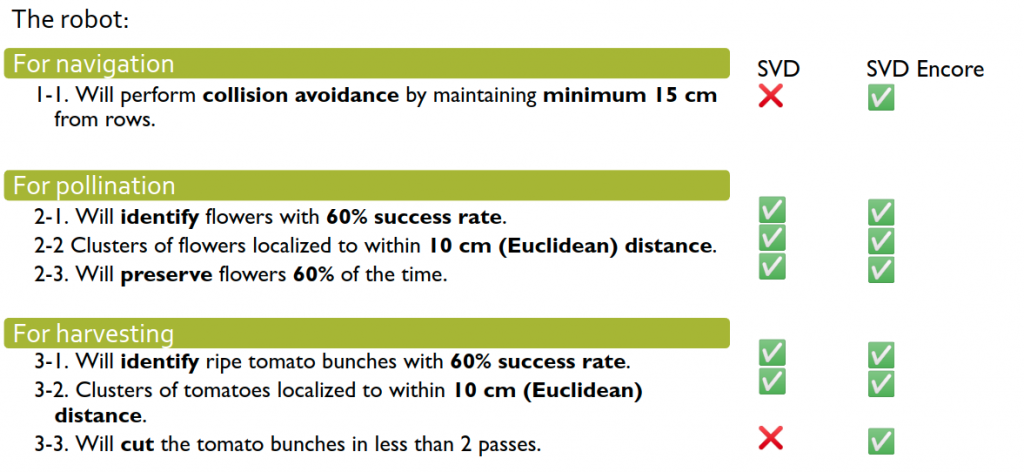